The waterproof performance and moisture-proof effect of acrylic solid surfaces need to be analyzed from three dimensions: the chemical structure of the material, the interface interaction mechanism, and the environmental interaction characteristics. Its protective efficacy should be verified in combination with laboratory tests and actual scenarios. The following is a systematic elaboration from three aspects: performance sources, test methods, and failure modes:
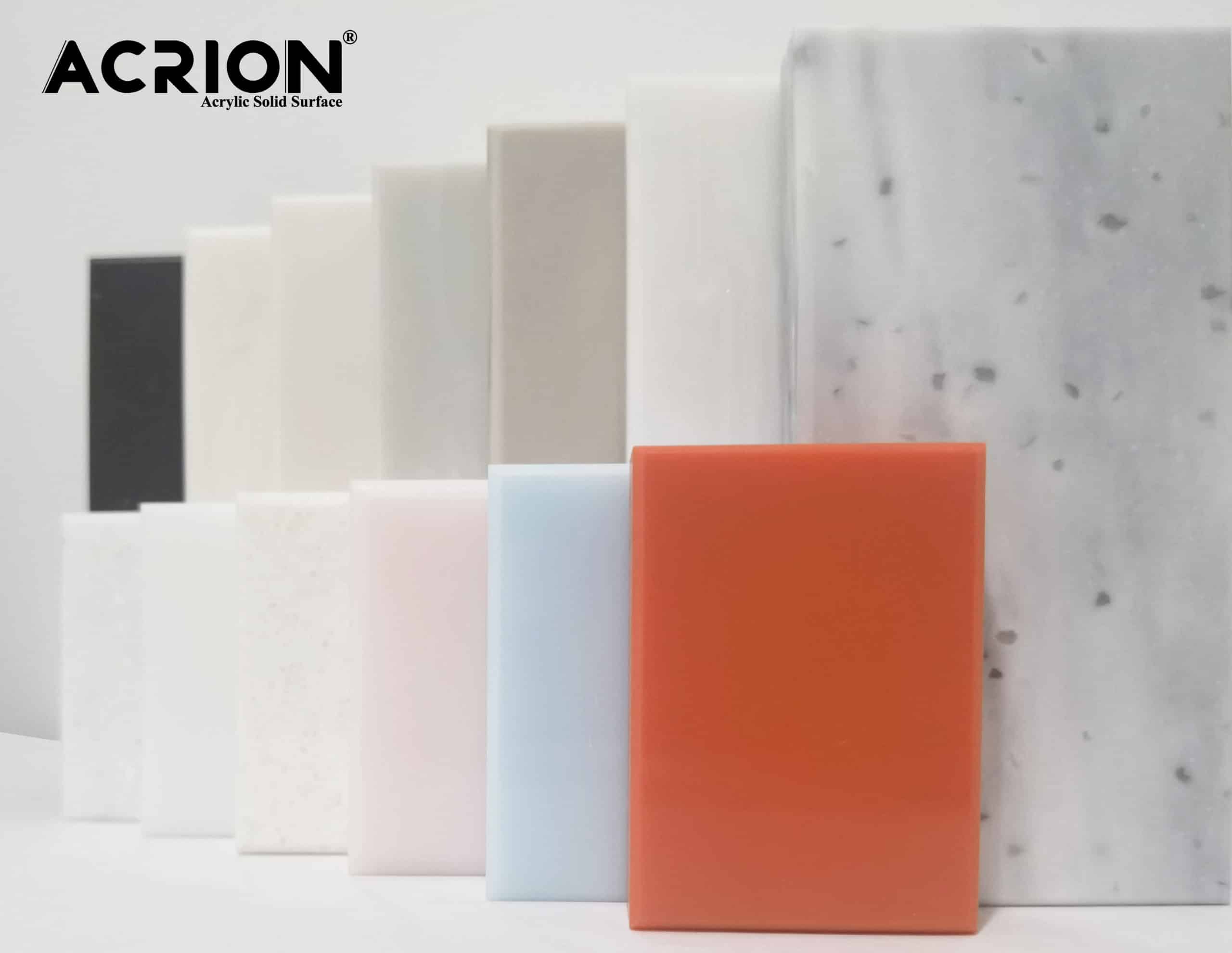
First, the chemical basis and structural characteristics of waterproof performance
Low surface energy characteristics
The polarity difference between the ester group (-COO-) and the alkyl chain (-CnH2n+1) in acrylic resin leads to a relatively weak intermolecular force, endowing the coating surface with a low surface energy of 15-30 mN/m. For instance, the water contact Angle of pure acrylic coating can reach 90°-105°, and the water droplets on the surface present a nearly spherical state, significantly reducing the tendency of wetting.
Cross-linked network structure
The three-dimensional cross-linked network formed by multi-functional monomers (such as trihydroxymethylpropane triacrylate) can prevent the penetration of water molecules. For instance, a coating with a crosslinking density of 80% can have its water absorption rate controlled below 0.5%, which is much lower than the 3%-5% of linear polymers.
Micro-nano structure construction
Superhydrophobic effects can be achieved by forming a rough structure of 50-200 nm on the coating surface through phase separation or template method. For instance, introducing fluoropolymer microphases into acrylic coatings can increase the water contact Angle to over 150° and the rolling Angle to less than 5°.
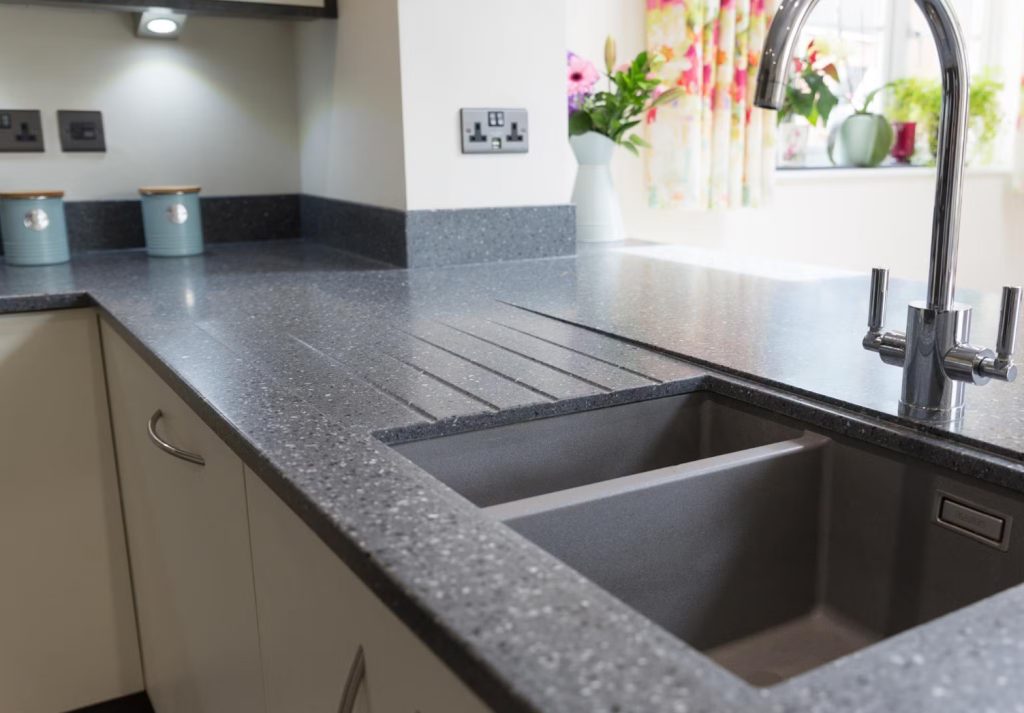
Second, the mechanism and influencing factors of moisture-proof effect
Water molecule diffusion barrier
The dense cross-linked structure can prolong the diffusion path of water molecules. For example, in an environment of 85%RH, the water vapor transmission rate (WVTR) of the cross-linked coating can be as low as 1 g/(m²·24h), while that of the uncross-linked coating may reach 5 g/(m²·24h).
The interfacial adhesion is balanced
The adhesion between the coating and the substrate needs to be greater than the adsorption energy of water molecules at the interface. For example, when the adhesion reaches 3 MPa, it can resist the interfacial penetration of water molecules within the range of -20℃ to 60℃, avoiding the phenomenon of debonding.
Environmental adaptability
Temperature changes will affect the expansion coefficient of the coating and the surface tension of water. For example, at -10℃, the kinetic energy of water molecules decreases, which may intensify the condensation in the micropores of the coating. At 40℃, the water vapor pressure increases, and a higher crosslinking density is required to maintain moisture resistance.
Third, the testing methods for waterproof and moisture-proof performance
Static contact Angle measurement
Using an optical contact Angle meter, 2 μL of deionized water was dropped in under the conditions of 25℃ and 50%RH, and the changes in the contact Angle within 30 seconds were recorded. For example, the initial contact Angle of high-quality acrylic coating can reach 100°, and the change is less than 2° within 60 seconds.
Dynamic water absorption experiment
Soak the coated sample in deionized water and weigh it regularly to record the quality changes. For example, after 24 hours of soaking, a coating with a water absorption rate lower than 0.8% can be regarded as having good water resistance. If the water absorption rate exceeds 2%, there may be micro-pore defects.
High humidity cycle test
Circulate for 24 hours between 85%RH and 40℃ and 25%RH and 20℃ for 100 consecutive times. Observe whether the coating shows blisters, discoloration or a decrease in adhesion. For example, if the adhesion decreases by no more than grade 1 after circulation (by the grid method).
Water vapor transmission rate test
According to the ASTM E96 standard, the WVTR was determined by the cup method or the infrared sensor method. For instance, under conditions of 38℃ and 90%RH, coatings with WVTR lower than 2 g/(m²·24h) are suitable for scenarios with high moisture-proof requirements.
Fourth, Failure Modes and improvement Strategies
Coating defects cause penetration
Pinholes or bubbles can cause local waterproofing failure. For example, pinholes with a diameter of 0.1mm can increase the overall water absorption rate of the coating by 30%. Improvement methods include optimizing the spraying process (such as increasing the atomization pressure to 0.3 MPa) or adopting multi-coat coating.
Interface debonding leads to failure
The adsorption of water molecules at the coating-substrate interface will weaken the adhesion. For instance, on a concrete substrate, if no primer treatment is carried out, the adhesion may decrease by 40% after six months. The solutions include using adhesion promoters or increasing the coating thickness to over 150 μm.
Chemical erosion damages the structure
Acidic and alkaline environments will accelerate the hydrolysis of the coating. For instance, after being immersed in an acidic solution with pH=2 for 72 hours, the cross-linking density of the coating may decrease by 25%. The improvement directions include introducing hydrolysis-resistant groups (such as siloxanes) or increasing the hardness of the coating to more than 2H.
Fifth, verification of actual application scenarios
Building exterior wall protection
In rainy areas, it is necessary to verify the coating’s resistance to rainwater erosion. For example, through a spray test simulating 10 years of rainfall (approximately 3000 mm), observe whether the coating shows powdering or peeling.
Packaging of electronic equipment
For high-humidity environments (such as 85%RH, 85℃), it is necessary to test the protective effect of the coating on the circuit board. For instance, after a 1000-hour test, the insulation resistance of the circuit board protected by the moisture-free coating should remain above 10¹² Ω.
Anti-corrosion of underground facilities
In the scenario of groundwater infiltration, it is necessary to evaluate the cathodic disbondment resistance of the coating. For example, after being maintained at a potential of -1.5V for 28 days, the peeling radius between the coating and the metal substrate should be less than 5 mm.