I. Einleitung
Das Solid Surface Thermoforming ist eine zentrale Technik im Bereich der Materialbearbeitung und bietet eine einzigartige Möglichkeit zur Herstellung komplizierter 3D-Kurven und abgerundeter Formen. Bei diesem Verfahren werden synthetische Materialien, insbesondere feste Oberflächen wie DuPont™ Corian®, erhitzt, um bemerkenswerte Designs zu erzielen, die mit Alternativen wie Quarz oder Granit ihresgleichen suchen.
Überblick über das Thermoformen fester Oberflächen
Der Prozess beginnt mit einer sorgfältigen Materialvorbereitung, um sicherzustellen, dass seine Abmessungen und sein Zustand den anspruchsvollen Kriterien des Thermoformvorgangs entsprechen. Die nachfolgenden Schritte, von der kontrollierten Erwärmung bis zum Präzisionsformen, verwandeln eine starre Platte in eine flexible Leinwand, die auf die Berührung durch den Künstler wartet.
Bedeutung und Anwendungen
Die Bedeutung des Solid-Surface-Thermoformens liegt in seiner Fähigkeit, maßgeschneiderte, dreidimensionale Meisterwerke herzustellen. Designer auf der ganzen Welt bevorzugen diese Technik wegen ihrer beispiellosen Freiheit, Formen und Bögen zu formen und so die Schaffung einzigartiger, optisch auffälliger Oberflächen zu ermöglichen. Ob bei Möbeln, Küchenarbeitsplatten oder Gewerbeflächen, das Thermoformen von Mineralwerkstoffen entwickelt sich zu einem Eckpfeiler im Bereich des modernen Designs und der Fertigung. Dieser Leitfaden befasst sich mit den Feinheiten dieses Transformationsprozesses und bietet Einblicke sowohl für Anfänger als auch für erfahrene Profis.
Das Thermoformen von festen Oberflächen ist eine weit verbreitete Technik im Bereich der Herstellung von festen Oberflächen und ermöglicht die Erstellung komplexer und individueller Designs. Bei diesem Prozess wird ein festes Oberflächenmaterial wie Acrion erhitzt und in die gewünschte Form gebracht. In diesem Leitfaden führen wir Sie Schritt für Schritt durch den Prozess der Thermoformung fester Oberflächen und geben dabei wichtige Hinweise und Vorsichtsmaßnahmen. Es ist wichtig, diese Richtlinien einzuhalten, die Eignung des Materials für den beabsichtigten Verwendungszweck zu prüfen und die geltenden Gesetze und Vorschriften einzuhalten.
II. Material vorbereitung
Materialübersicht
Bei der Thermoformung fester Oberflächen kommt es auf eine sorgfältige Materialauswahl an, wobei vorwiegend Platten auf Acrylbasis wie DuPont™ Corian® zum Einsatz kommen. Diese Materialien bieten ein empfindliches Gleichgewicht zwischen Flexibilität und Haltbarkeit, was für die Erzielung der gewünschten Formen während des Thermoformprozesses von entscheidender Bedeutung ist. Das Verständnis der spezifischen Eigenschaften des ausgewählten Materials ist von größter Bedeutung, da jede Marke beim Erhitzen und Formen ein unterschiedliches Verhalten zeigen kann.
Materialfähigkeit und Vorbereitung
Der Erfolg des Thermoformens hängt in hohem Maße von einer präzisen Materialvorbereitung ab. Der Prozess beginnt mit Blechzuschnitten, die geringfügig größer als die Endabmessungen sind, und berücksichtigt die Materialschrumpfung nach dem Erhitzen. Darüber hinaus ist die Beseitigung von Mängeln wie Absplitterungen oder Kratzern unerlässlich, da diese Mängel als Auslöser für Risse im geformten Material dienen können. Das Erreichen einer glatten, fehlerfreien Oberfläche gewährleistet ein einwandfreies Endprodukt und minimiert das Risiko struktureller Schwachstellen.
Für die Materialvorbereitung erforderliche Werkzeuge
Voraussetzung für eine effektive Materialvorbereitung ist die Bewaffnung mit den entsprechenden Werkzeugen. Zu den wesentlichen Instrumenten gehören Präzisionsschneidwerkzeuge zur Erzielung präziser Abmessungen, Schleifgeräte für makellose Kanten sowie Sicherheitsausrüstung wie Handschuhe und Augenschutz zum Schutz vor potenziellen Gefahren. Ein gut vorbereiteter Arbeitsplatz, der mit diesen Werkzeugen ausgestattet ist, bildet die Grundlage für eine reibungslose Materialvorbereitungsphase. Das Streben nach Perfektion in diesem ersten Schritt schafft die Voraussetzungen für ein erfolgreiches Thermoformungsvorhaben, bei dem die Liebe zum Detail zum Synonym für qualitativ hochwertige Ergebnisse wird.
III. Erhitzen von festen Oberflächenmaterialien
A. Vorheizen
Allgemeine Informationen:
Das Vorwärmen schafft die Voraussetzungen für eine erfolgreiche Thermoformung fester Oberflächen. Es ist von grundlegender Bedeutung, das Verhalten des Materials in dieser kritischen Phase zu verstehen. Das Vorwärmen gewährleistet eine gleichmäßige Flexibilität und macht den nachfolgenden Formgebungsprozess vorhersehbarer.
Heizmethoden (Öfen, Infrarot usw.):
Es werden verschiedene Heizmethoden eingesetzt, von denen jede ihre Vorzüge hat. Plattenöfen bieten direkten Kontakt und ermöglichen so eine schnellere Erwärmung, während Umluftöfen für eine kontrolliertere Umgebung sorgen. Infrarot-Optionen werden zwar nicht empfohlen, sind aber für ungefüllte Kunststoffe geeignet. Um Präzision und Konsistenz zu gewährleisten, ist die Kalibrierung des gewählten Ofens unerlässlich.
Kalibrieren des Ofens:
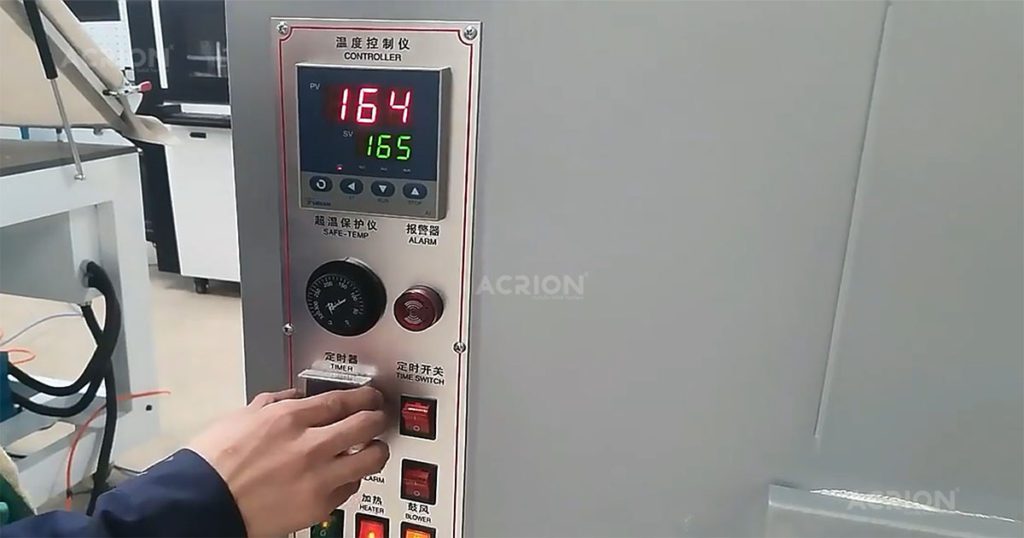
Die Ofenkalibrierung ist ein sorgfältiger Prozess. Durch die Festlegung und Überprüfung der Temperatureinstellungen wird sichergestellt, dass das Material genau erhitzt wird. Die Häufigkeit der Kalibrierung, insbesondere in Umgebungen mit hoher Produktion, garantiert optimale Leistung und zuverlässige Thermoformergebnisse.
B. Materialflexibilität
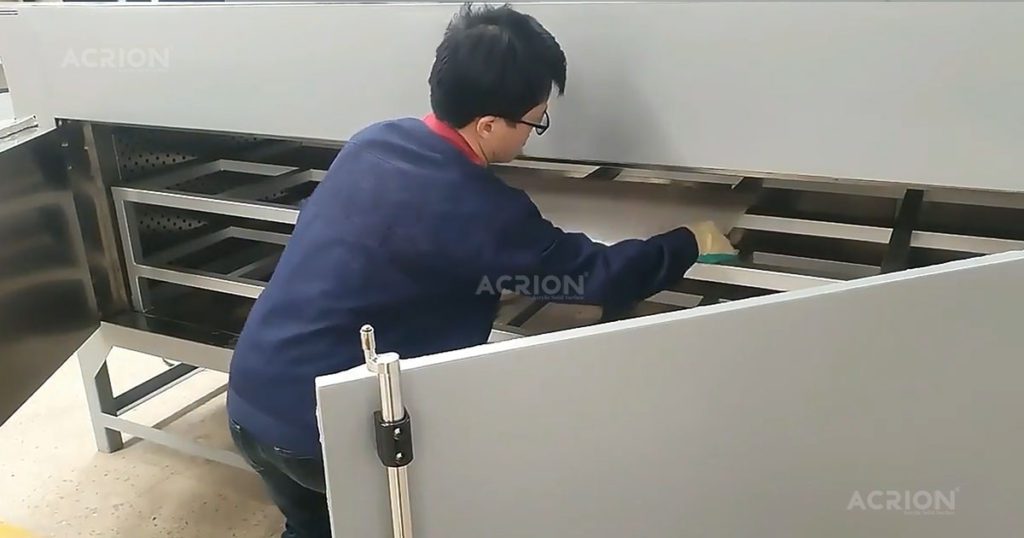
Faktoren, die die Materialflexibilität beeinflussen:
Die Materialflexibilität wird von mehreren Faktoren beeinflusst. Dabei spielen Dicke, Zusammensetzung und Vorwärmdauer eine entscheidende Rolle. Das Verständnis dieser Variablen ermöglicht maßgeschneiderte Anpassungen und optimiert die Flexibilität für spezifische Thermoformanforderungen.
Techniken zur Verbesserung der Materialflexibilität:
Die Maximierung der Materialflexibilität erfordert strategische Ansätze. Das gezielte Ausdünnen oder Falzen des Materials, insbesondere bei komplizierten Designs, kann die Flexibilität verbessern, ohne die strukturelle Integrität zu beeinträchtigen. Darüber hinaus gewährleistet die Optimierung der Heiztemperaturen basierend auf der Materialzusammensetzung einen biegsamen und dennoch elastischen Zustand.
Schummeln
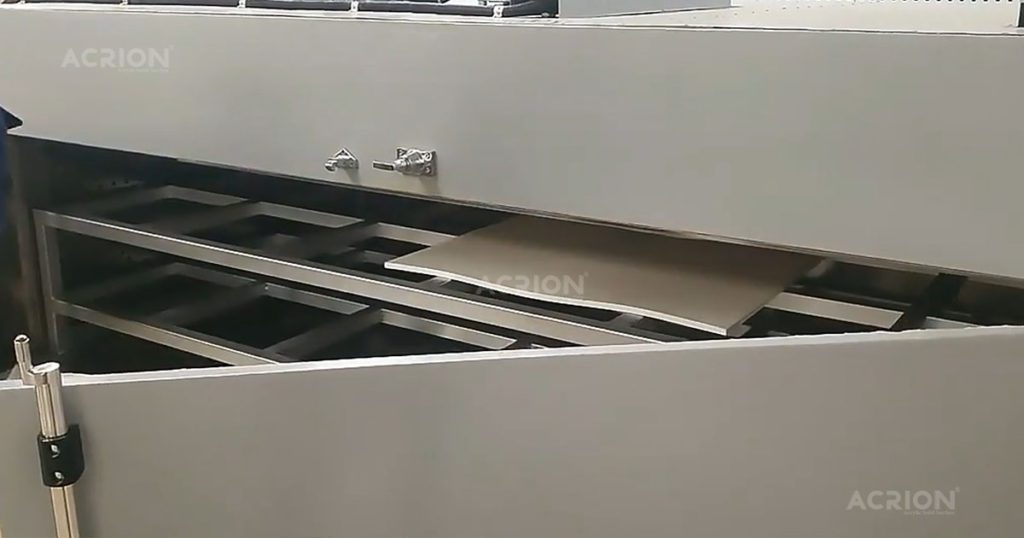
Verschiedene Heizansätze:
Die Thermoformlandschaft bietet vielfältige Erwärmungsansätze. Während Plattenöfen einen schnellen, direkten Kontakt ermöglichen, basieren Umluftöfen auf einem langsameren, kontrollierten Prozess. Aus Effizienzgründen können höhere Temperaturen verwendet werden, es ist jedoch Vorsicht geboten, um eine Überhitzung zu verhindern, die die Materialintegrität beeinträchtigen kann.
Temperaturmessung und -regelung:
Eine präzise Temperaturkontrolle ist nicht verhandelbar. Unabhängig davon, ob Kontaktthermoelemente, Infrarot-Thermometer oder andere fortschrittliche Methoden verwendet werden, ist die Überwachung und Aufrechterhaltung der gewünschten Temperatur während der gesamten Aufheizphase von entscheidender Bedeutung. Diese sorgfältige Kontrolle gewährleistet eine gleichmäßige Materialbereitstellung für die nachfolgenden Formungsschritte.
IV. Biegen und Formen
Techniken zum Biegen und Formen
Effiziente Biegetechniken:
Das Biegen von Mineralwerkstoffen erfordert Präzision und Fingerspitzengefühl. Entscheidend ist der Einsatz kontrollierter Kraft und die Nutzung der während der Aufheizphase erreichten Flexibilität des Materials. Techniken wie Kantenbiegen, Drapieren und Freiblasen werden auf unterschiedliche Projektanforderungen zugeschnitten. Diese Methoden gewährleisten eine gleichmäßige Formgebung und verringern gleichzeitig das Risiko von Deformitäten.
Formprozess:
Das Formen ist der Grundstein für eine erfolgreiche Thermoformung fester Oberflächen. Durch die Verwendung männlicher und weiblicher Formen aus Materialien wie Sperrholz oder MDF entsteht ein strukturierter Rahmen, an den sich das Material beim Abkühlen anpassen kann. Sorgfältige Beachtung des Formendesigns unter Berücksichtigung von Entformungsschrägen und Teilefreigabe garantiert optimale Ergebnisse im Endprodukt.
Formgebungsansätze (Vakuumpressen, hydraulisches Pressen)
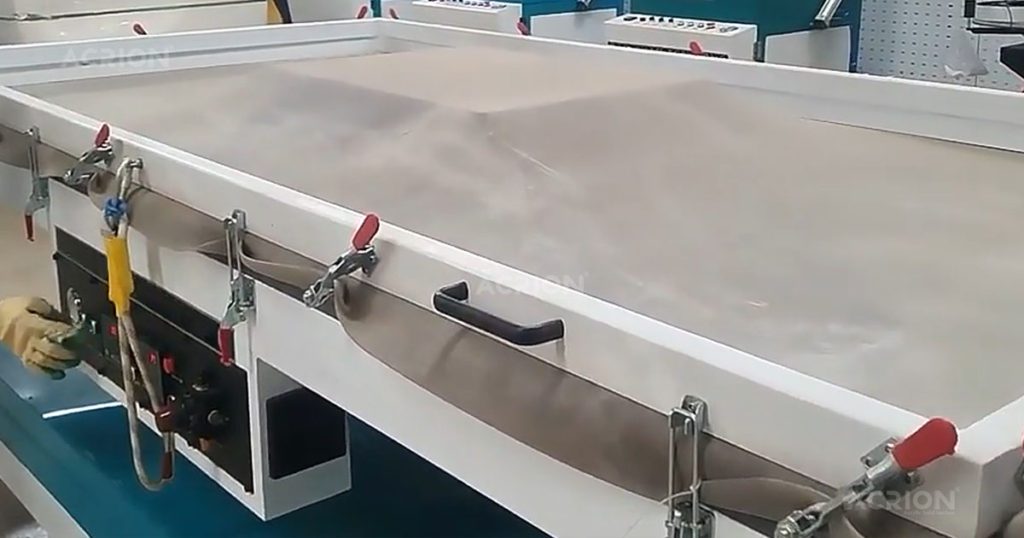
Vakuumpressen für Präzision:
Vakuumpressen ist aufgrund seiner Präzision und Vielseitigkeit ein beliebter Ansatz. Bei diesem Verfahren wird das erhitzte Material mit einer Vakuummembranpresse auf die Formoberfläche gezogen und so sichergestellt, dass auch komplizierte Details originalgetreu reproduziert werden. Diese Methode ist besonders effektiv bei komplexen Designs und wird aufgrund ihrer Effizienz in der Großserienproduktion häufig eingesetzt.
Hydraulisches Pressen für strukturelle Integrität:
Das hydraulische Pressen bietet eine robuste Lösung zum Formen fester Oberflächenmaterialien mit verbesserter struktureller Integrität. Die Druckausübung über hydraulische Systeme sorgt für eine gleichmäßige Kompression und minimiert das Risiko von Verformungen. Dieser Ansatz wird für Projekte bevorzugt, bei denen Haltbarkeit und Maßhaltigkeit im Vordergrund stehen, wie z. B. Architekturelemente und Industriekomponenten.
Der Erfolg des Thermoformens von festen Oberflächen hängt von der nahtlosen Integration dieser Biege- und Formtechniken ab. Durch die Auswahl der geeigneten Methode auf der Grundlage der Projektspezifikationen und Materialeigenschaften können Hersteller eine außergewöhnliche Präzision und Konsistenz im Endprodukt erzielen.
V. Formen und Formen
Arten von Formen
1. Männliche und weibliche Formen:
Die grundlegende Dichotomie bei den Formentypen besteht darin, dass männliche Formen in das Material hineinragen, während weibliche Formen das Material umhüllen und formen. Patrizenformen werden oft für flache Kurven verwendet, während Matrizenformen ideal für komplizierte Designs sind. Die Wahl des richtigen Typs hängt vom gewünschten Ergebnis und der Reaktion des Materials auf Verformungskräfte ab.
2. Passende Formen:
Aufeinander abgestimmte Formen, bei denen beide Hälften präzise ineinandergreifen, sorgen für eine gleichmäßige Druckverteilung beim Formen. Diese sorgfältige Ausrichtung minimiert das Fehlerrisiko und verbessert die Gesamtqualität des geformten Mineralwerkstoffs. Passende Formen werden für komplizierte Geometrien und kritische Abmessungen bevorzugt.
Überlegungen zum Formendesign
1. Schrägenwinkel:
Die Einbeziehung von Entformungsschrägen in die Formenkonstruktion ist für eine erfolgreiche Teilefreigabe von entscheidender Bedeutung. Diese leichten Verjüngungen erleichtern die einfache Entnahme des geformten Materials aus der Form und verringern so die Wahrscheinlichkeit einer Beschädigung. Strategische Entformungsschrägen tragen auch zu einer glatteren Oberflächenbeschaffenheit des Endprodukts bei.
2. Trennlinien:
Trennlinien markieren die Trennung zwischen Formhälften. Die Sicherstellung einer präzisen Ausrichtung und minimaler Abweichung entlang der Trennlinien ist entscheidend für die Erzielung einer Nahtlosigkeit im geformten Material. Die Beachtung der Details der Trennlinien vermeidet Unvollkommenheiten und verbessert die Gesamtästhetik.
Vorbereitung und Verwendung von Formen
1. Oberflächenbehandlung:
Vor der Verwendung sollten Formen einer sorgfältigen Oberflächenbehandlung unterzogen werden. Dies kann Polieren, Beschichten oder das Auftragen von Trennmitteln umfassen, um die Materialfreisetzung zu optimieren und ein Anhaften zu verhindern. Eine gut behandelte Formoberfläche führt zu einem makellosen Finish auf der thermogeformten festen Oberfläche.
2. Überlegungen zur Temperatur:
Die Aufrechterhaltung einer optimalen Formtemperatur ist von größter Bedeutung. Abweichungen können sich auf die Abkühlgeschwindigkeit des Materials und damit auf seine Endeigenschaften auswirken. Das Vorwärmen von Formen, insbesondere bei sequentiellen Formungsprozessen, sorgt für konsistente Ergebnisse, indem Schwankungen bei Abkühlzeiten und Teileabmessungen minimiert werden.
Formen und Gussformen bilden das Rückgrat des Thermoformprozesses für feste Oberflächen. Sorgfältige Auswahl, präzises Design und gründliche Vorbereitung der Formen sind unverzichtbare Elemente, um die gewünschte Form und Oberfläche im Endprodukt zu erreichen.
WIR. Abkühlen
Bedeutung der Kühlung
Eine effiziente Kühlung ist eine entscheidende Phase im Thermoformungsprozess für feste Oberflächen und formt die endgültigen Eigenschaften des Materials. Die Abkühlphase dient dem Abbau innerer Spannungen und der Verfestigung der gebildeten Struktur. Die richtige Kühlung ist entscheidend für das Erreichen der gewünschten Maßgenauigkeit und die Vermeidung von Verformungen im Endprodukt.
Cool-Down-Techniken
1. Kontrollierte Umgebung:
Die Durchführung des Kühlprozesses in einer kontrollierten Umgebung sorgt für Gleichmäßigkeit. Dazu gehört die Abschwächung externer Faktoren wie Luftstrom, Temperaturschwankungen und Zugluft, die sich negativ auf die Kühlrate auswirken können. Eine stabile Umgebung trägt zu einer gleichbleibenden Teilequalität bei.
2. Allmähliche Abkühlung:
Eine allmähliche Abkühlung ist unbedingt erforderlich, um einen Thermoschock zu vermeiden und die strukturelle Integrität aufrechtzuerhalten. Abrupte Temperaturänderungen können zu Verformungen, Rissen oder Oberflächenunregelmäßigkeiten führen. Der Einsatz eines systematischen Kühlansatzes, sei es durch Umgebungsluft oder kontrollierte Kammern, erhöht die Gesamtstabilität des Materials.
Dauer und Überlegungen beim Abkühlen
1. Einfluss der Materialstärke:
Die Abkühldauer wird durch die Dicke des festen Oberflächenmaterials beeinflusst. Dickere Abschnitte erfordern längere Abkühlzeiten, um eine gründliche Erstarrung zu gewährleisten. Das Ausbalancieren der Abkühldauer und der Materialstärke ist entscheidend, um ein vorzeitiges Entfernen aus den Formen zu verhindern und das Risiko einer Verformung zu verringern.
2. Inspektion nach dem Abkühlen:
Nach der vorgesehenen Abkühlzeit ist eine sorgfältige Kontrolle unerlässlich. Durch die Überprüfung, ob das Material die vorgeschriebene Temperatur erreicht und sich ausreichend abgesetzt hat, können rechtzeitig Anpassungen vorgenommen werden. Diese sorgfältige Prüfung verringert das Risiko einer vorzeitigen Handhabung des Materials und bewahrt die gewünschte Form und strukturelle Integrität.
Die Kühlung, ein oft unterschätzter Aspekt, ist entscheidend für den Erfolg des Thermoformens von Festkörperoberflächen. Der Einsatz sorgfältiger, auf Materialstärke und Umgebungsbedingungen abgestimmter Kühltechniken gewährleistet die Herstellung einwandfreier, formstabiler Thermoformteile.
VII. Letzter Schliff
Nahttechniken
Präzision in der Tischlerei:
Das Nähen beim Thermoformen mit fester Oberfläche erfordert viel Liebe zum Detail. Um nahtlose Verbindungen zu erreichen, ist Präzision beim Schneiden und Ausrichten der Teile erforderlich. Die Verwendung spezieller Klebstoffe für feste Oberflächenmaterialien sorgt für robuste, unauffällige Nähte. Eine gründliche Reinigung und Vorbereitung der Verbindungsflächen verbessert die Klebeverbindung und trägt so zur strukturellen Integrität der Endmontage bei.
Trimmen und Endbearbeitung
Maßgenauigkeit nach dem Formen:
Beschnitt- und Endbearbeitungsvorgänge sind unerlässlich, um thermogeformte Teile entsprechend ihren beabsichtigten Spezifikationen zu verfeinern. Mithilfe von Präzisionsschneidwerkzeugen und -techniken entfernen die Bediener vorsichtig überschüssiges Material und bringen die Kanten wieder in die gewünschte Form. Die konsequente Liebe zum Detail in dieser Phase stellt die Wahrung der Designabsicht und der Gesamtmaßgenauigkeit sicher.
Qualitätskontrolle
Strenge Bewertungsstandards:
Die Qualitätskontrolle dient als letzter Kontrollpunkt im Thermoformprozess für feste Oberflächen. Es werden strenge Inspektionsprotokolle implementiert, um die visuelle Ästhetik, die strukturelle Solidität und die Einhaltung der Designspezifikationen zu beurteilen. Eventuelle Abweichungen von den vorgegebenen Standards werden zeitnah erkannt und behoben. Dieser sorgfältige Qualitätssicherungsprozess garantiert die Lieferung einwandfreier, qualitativ hochwertiger thermogeformter Produkte an den Endverbraucher.
In den letzten Phasen des Thermoformens von festen Oberflächen liegt der Schwerpunkt auf Präzision auch beim Falzen, Beschneiden und der Qualitätskontrolle. Die Einhaltung anspruchsvoller Standards in diesen abschließenden Schritten führt zu professionell gefertigten Produkten, die die Designerwartungen erfüllen oder übertreffen.
VIII. Öfen
Übersicht über verschiedene Öfen
Beim Thermoformen fester Oberflächen ist die Auswahl des geeigneten Ofens eine entscheidende Entscheidung. Drei Haupttypen – Infrarot/Strahlung, Heißluft/Konvektion und Plattenpresse – bieten unterschiedliche Heizmechanismen. Infrarotöfen dringen effizient in ungefüllte Kunststoffe ein, während Heißluftöfen für eine gleichmäßige Erwärmung sorgen. Plattenpressöfen, die direkten Kontakt mit den Materialseiten haben, beschleunigen den Erhitzungsprozess. Eine sorgfältige Prüfung der Projektanforderungen leitet die Auswahl und gewährleistet optimale Ergebnisse.
Kalibrierung von Öfen
Die Ofenkalibrierung ist ein kritischer Aspekt, der oft übersehen wird. Für ein erfolgreiches Thermoformen ist eine präzise Temperaturkontrolle unerlässlich. Durch regelmäßige Kalibrierungsprüfungen wird sichergestellt, dass die tatsächliche Temperatur des Ofens mit dem Sollwert übereinstimmt, wodurch die Konsistenz über mehrere Zyklen hinweg gewährleistet wird. Ein gut kalibrierter Ofen minimiert das Risiko einer Überhitzung oder Unterhitzung und gewährleistet die Integrität der Platten mit fester Oberfläche während des Thermoformprozesses.
Best Practices für die Verwendung im Ofen
Eine effiziente Ofennutzung erfordert strategische Planung und die Einhaltung bewährter Verfahren. Um optimale Ergebnisse zu erzielen, heizen Sie den Ofen auf die gewünschte Formtemperatur vor und achten Sie auf Stabilität, bevor Sie mit dem Prozess beginnen. Die Sicherheit und die Verfügbarkeit der notwendigen Ausrüstung sind von größter Bedeutung. Während Hersteller möglicherweise versucht sind, die Ofentemperaturen zu erhöhen, um das Aufheizen zu beschleunigen, ist es wichtig, die empfohlenen Grenzwerte einzuhalten – eine Überschreitung von 205 °C (400 °F) birgt Risiken. Darüber hinaus unterstützt das Nacherhitzen, indem man den thermogeformten Rohling ein bis zwei Minuten lang ruhen lässt, den Temperaturausgleich vor dem Formentransfer, ein Schritt, der oft unterschätzt wird, aber für erfolgreiche Thermoformergebnisse von entscheidender Bedeutung ist.
Wenn Sie sich in der Welt des Thermoformens von festen Oberflächen zurechtfinden, tragen das Verständnis der Nuancen verschiedener Öfen, eine sorgfältige Kalibrierung und die Einhaltung etablierter Best Practices gemeinsam zu einem optimierten und effektiven Thermoformprozess bei.
IX. Thermoformungsspezifikationen für verschiedene Marken von Solid Surface
Vergleich der Thermoformanforderungen verschiedener Marken
Die Thermoformspezifikationen variieren je nach Solid-Surface-Marke und wirken sich auf die Erhitzungs-, Biege- und Formprozesse aus. Nachfolgend finden Sie einen umfassenden Vergleich der Thermoformanforderungen für 12 bekannte Marken:
Marke | Heiztemperatur | Erhitzungszeit | Materialstärke | Kühlzeit | Besondere Überlegungen |
Corian | 160°C – 170°C | 25 – 35 Min | 12 mm (1/2″) | 45 Min | Bei dunklen Farben kann es zu Farbveränderungen kommen |
Akrion | 160°C – 170°C | 20 – 30 Minuten | 12 mm (1/2″) | 40 Min | Eine gründliche Kühlung ist entscheidend für die Formerhaltung |
Tristone | 150°C | 15 – 20 Minuten | 9 mm (3/8″) | 30 Minuten | Ermöglicht die Erstellung fließender Designs |
Wilson-Kunst | 160°C | 25 – 35 Min | 12 mm (1/2″) | 40 Min | Entscheidend ist die ordnungsgemäße Erwärmung des gesamten Blechs |
Crion | 285°F | 18 Min | 12 mm (1/2″) | 30 Minuten | Thermoformverfahren für komplizierte Designs |
LG Hausys | 155°C – 165°C | 20 – 30 Minuten | 6 mm (1/4″) | 35 Min | Transparente Partikel lassen sich möglicherweise nicht gut thermoformen |
Starron | 150°C | 18 – 25 Min | 9 mm (3/8″) | 30 Minuten | Geeignet zum Erstellen von 3D-Formen |
Hanex | 160°C – 170°C | 25 – 35 Min | 12 mm (1/2″) | 40 Min | Eine gründliche Kühlung ist entscheidend für die Formerhaltung |
Meganit | 155°C – 160°C | 20 – 30 Minuten | 6 mm (1/4″) | 35 Min | Die Materialflexibilität hängt von der jeweiligen Mischung ab |
Aristech-Oberflächen | 160°C | 25 – 35 Min | 12 mm (1/2″) | 40 Min | Beim Thermoformen dunkler Farben ist Vorsicht geboten |
Durasein | 155°C – 165°C | 20 – 30 Minuten | 6 mm (1/4″) | 40 Min | Nicht für horizontale Anwendungen geeignet |
Die Thermoformungsspezifikationen für verschiedene Solid-Surface-Marken variieren und weisen unterschiedliche Temperatur-, Zeit- und Materialaspekte auf. Um optimale Ergebnisse zu erzielen, müssen Handwerker die spezifischen Anforderungen jeder Marke sorgfältig auswählen und einhalten. Die obige Tabelle bietet eine Kurzanleitung, die Fachleuten dabei hilft, sich in den unterschiedlichen Spezifikationen beliebter Solid-Surface-Marken im Thermoformprozess zurechtzufinden.
X. Prozessentwicklung und Fehlerbehebung
Beispiel eines Prozessprotokolls
• Material (Farbe und Stärke)
• Gebrauchsprozedur
• Leere Vorlage oder Programm
• Ofentemperatur
• Form-ID
• Formtemperatur (vorher und nachher)
• Aufheiz- und Abkühlzeit
• Gerät oder Programm trimmen
• Anzahl der mit der Form hergestellten Teile
• Tageszeit
• Umgebungstemperatur
• Operator
• Erfolg oder Misserfolg
• Verwendete Prozesshilfsmittel (Talkum, Wachs etc.)
Eine sorgfältige Prozessaufzeichnung ist der Grundstein für ein erfolgreiches Unternehmen im Bereich der Thermoformung fester Oberflächen. Durch die Dokumentation kritischer Parameter wie Materialdetails, Betriebsabläufe, Ofenspezifikationen und Formungsfeinheiten entsteht eine Roadmap für Konsistenz. Zu den Schlüsselelementen gehören Materialfarbe und -dicke, Aufheiz- und Abkühlzeiten, Formeigenschaften und Angaben zum Bediener. Dieses umfassende Protokoll sorgt nicht nur für Einheitlichkeit, sondern wird auch zu einer unschätzbar wertvollen Ressource für die Identifizierung von Technikänderungen im Laufe der Zeit.
Optimierung des Thermoformprozesses
Die Steigerung der Produktionsraten erfordert einen strategischen Ansatz, der auf dem Verständnis der limitierenden Faktoren basiert. Ganz gleich, ob Sie einen Plattenofen für mehrere Formen oder einen Umluftofen für eine einzelne Form verwenden, jeder hat seine Vorzüge. Die Anpassung der Umformtemperatur beeinflusst die Materialsteifigkeit und ermöglicht so die Kontrolle über natürliche Lichtbögen. Die Minimierung der Verformung ist von entscheidender Bedeutung – das Gleiten des Materials gegenüber der Dehnung zu bevorzugen und die Kompression gegenüber der Dehnung zu bevorzugen, sorgt für optimale Ergebnisse. Die Untersuchung von Kompromissen beim Formmaterial, Farbverschiebungen beim Erhitzen und vorbeugende Maßnahmen wie das Erhitzen flacher Bleche tragen alle zu einem optimierten Thermoformprozess bei.
Beheben häufiger Probleme
Herausforderungen beim Thermoformen erfordern einen systematischen Ansatz zur Fehlerbehebung. Eine Weißfärbung, die oft auf eine unzureichende Temperatur zurückzuführen ist, erfordert eine gründliche Prüfung der Sollwerte, der Ofenfunktionalität und der Vorheizbedingungen. Die Oberflächenkühlung vor der Umformung erfordert ein sorgfältiges Zeitmanagement. Das Überschreiten der maximalen Auszüge erfordert die Beurteilung der Biegefestigkeit, des Dehnungsgrads und des möglichen Einklemmens des Rohlings. Um Faltenbildung zu bekämpfen, müssen die Kompressionsgrade und das Formdesign überprüft werden. Ein Einreißen kann durch die Qualität der leeren Kanten, das Einklemmen oder die Überschreitung der Farbkapazitäten verursacht werden. Das Schleifen der Oberfläche erfordert eine schnelle Bewertung der Formoberfläche, wobei größere Partikelfarben eine sorgfältige Prüfung erfordern.
Zusammenfassend lässt sich sagen, dass die Beherrschung des Thermoformprozesses für feste Oberflächen nicht nur ein theoretisches Verständnis, sondern auch die Verpflichtung zur Dokumentation, Optimierung und Fehlerbehebung erfordert. Ein differenziertes Verständnis dieser Aspekte versetzt Hersteller in die Lage, Herausforderungen zu meistern und stets qualitativ hochwertige thermogeformte Produkte zu liefern.
XI. Sicherheitsaspekte
Schutzausrüstung
Die Gewährleistung einer sicheren Thermoformumgebung beginnt mit der sorgfältigen Auswahl und Verwendung der Schutzausrüstung. Hersteller müssen strenge Sicherheitsprotokolle einhalten, einschließlich der obligatorischen Verwendung von hitzebeständigen Handschuhen, Augenschutz und flammhemmender Kleidung. Ein gut belüfteter Arbeitsplatz, der mit geeigneter persönlicher Schutzausrüstung (PSA) ausgestattet ist, verringert das Risiko von Verbrennungen, Abschürfungen und der Belastung durch schädliche Dämpfe. Um ein sicheres Arbeitsumfeld zu gewährleisten, ist es unerlässlich, der konsequenten Verwendung und Wartung von Schutzausrüstung Priorität einzuräumen.
Standortsicherheitsrichtlinien
Die Festlegung standortspezifischer Sicherheitsrichtlinien ist für die Minimierung der mit der Thermoformung fester Oberflächen verbundenen Gefahren von größter Bedeutung. Arbeitsbereiche müssen mit Notausgängen, Feuerlöschausrüstung und Erste-Hilfe-Stationen ausgestattet sein, die strategisch günstig für einen schnellen Zugang angeordnet sind. Eine klare Beschilderung mit detaillierten Sicherheitsprotokollen, Notfallkontaktinformationen und Verfahrensanweisungen verbessert das Situationsbewusstsein. Darüber hinaus stellen regelmäßige Sicherheitsübungen und Schulungen sicher, dass das Personal mit den Notfallmaßnahmen vertraut ist. Die proaktive Umsetzung von Sicherheitsmaßnahmen, gepaart mit kontinuierlicher Schulung, bildet den Grundstein für eine sichere Arbeitsumgebung in Anlagen zum Thermoformen von Mineralwerkstoffen.
XII. Abschluss
Zusammenfassung der wichtigsten Schritte
Zusammenfassend lässt sich sagen, dass die Beherrschung des Thermoformprozesses für feste Oberflächen eine sorgfältige Herangehensweise erfordert, von der Materialvorbereitung bis zum letzten Schliff. Hersteller müssen beim Materialschneiden auf Präzision achten, optimale Heiztechniken einhalten und umsichtige Formgebungsmethoden anwenden. Der Einsatz gut konzipierter Formen, effektiver Kühlstrategien und ein wachsames Auge auf den letzten Schliff, einschließlich Nähten und Qualitätskontrolle, gewährleisten die Herstellung einwandfreier thermogeformter Oberflächen.
Zukünftige Trends beim Thermoformen fester Oberflächen
Mit Blick auf die Zukunft stehen dem Bereich der Thermoformung fester Oberflächen erhebliche Fortschritte bevor. Innovationen in der Materialzusammensetzung gepaart mit modernsten Heiztechnologien versprechen eine höhere Flexibilität und Effizienz im Thermoformprozess. Automatisierungs- und künstliche Intelligenzanwendungen können die Produktion rationalisieren und zu schnelleren Durchlaufzeiten und höherer Präzision führen. Da Umweltaspekte immer wichtiger werden, können Sie davon ausgehen, dass die Branche umweltfreundliche Materialien und nachhaltige Praktiken erforscht und sich damit der breiteren Bewegung hin zu umweltfreundlicheren Herstellungsprozessen anschließt. Verarbeiter, die diese aufkommenden Trends im Auge behalten, sind gut aufgestellt, um in der dynamischen Landschaft des Thermoformens von festen Oberflächen hervorzustechen.