I. Giới thiệu
Solid Surface Thermoforming là một kỹ thuật then chốt trong lĩnh vực thao tác vật liệu, mang đến một con đường độc đáo để tạo các đường cong 3-D phức tạp và các hình tròn. Quá trình này bao gồm việc nung nóng các vật liệu tổng hợp, đặc biệt là các bề mặt rắn như DuPont™ Corian®, để đạt được những thiết kế vượt trội mà các vật liệu thay thế như thạch anh hoặc đá granit không thể so sánh được.
Tổng quan về ép nóng bề mặt rắn
Quá trình bắt đầu với việc chuẩn bị vật liệu tỉ mỉ, đảm bảo kích thước và tình trạng của vật liệu đáp ứng các tiêu chí khắt khe của hành trình ép nóng. Các giai đoạn tiếp theo, từ gia nhiệt có kiểm soát đến đúc khuôn chính xác, biến một tấm vải cứng thành một tấm canvas linh hoạt đang chờ nghệ sĩ chạm vào.
Tầm quan trọng và ứng dụng
Tầm quan trọng của việc tạo hình nhiệt bề mặt rắn nằm ở khả năng tạo ra những kiệt tác ba chiều theo yêu cầu riêng. Các nhà thiết kế trên toàn thế giới ưa chuộng kỹ thuật này vì sự tự do tuyệt vời của nó trong việc điêu khắc các hình dạng và đường cung, cho phép tạo ra các bề mặt độc đáo, nổi bật về mặt thị giác. Cho dù trong đồ nội thất, mặt bàn bếp hay không gian thương mại, việc tạo hình nhiệt bề mặt rắn nổi lên như một nền tảng trong lĩnh vực thiết kế và chế tạo hiện đại. Hướng dẫn này đi sâu vào những điểm phức tạp của quá trình biến đổi này, cung cấp thông tin chi tiết cho cả người mới bắt đầu và các chuyên gia dày dạn kinh nghiệm.
Tạo hình bằng nhiệt bề mặt rắn là một kỹ thuật được sử dụng rộng rãi trong lĩnh vực chế tạo bề mặt rắn, cho phép tạo ra các thiết kế phức tạp và tùy chỉnh. Quá trình này liên quan đến việc làm nóng vật liệu bề mặt rắn, chẳng hạn như Acrion, và định hình nó thành các dạng mong muốn. Trong hướng dẫn này, chúng tôi sẽ hướng dẫn bạn từng bước quy trình tạo hình bằng nhiệt bề mặt rắn, cung cấp các lưu ý và biện pháp phòng ngừa quan trọng trong suốt quá trình. Điều quan trọng là phải tuân thủ các nguyên tắc này, xem xét tính phù hợp của tài liệu cho mục đích sử dụng của bạn và tuân thủ các luật và quy định hiện hành.
II. Chuẩn bị vật liệu
Tổng quan về vật liệu
Solid Surface Thermoforming phụ thuộc vào việc lựa chọn vật liệu tỉ mỉ, chủ yếu sử dụng các tấm gốc acrylic như DuPont™ Corian®. Những vật liệu này mang lại sự cân bằng tinh tế giữa tính linh hoạt và độ bền, điều này rất quan trọng để đạt được hình dạng mong muốn trong quá trình tạo hình nhiệt. Hiểu các đặc tính cụ thể của vật liệu được chọn là điều tối quan trọng, vì mỗi thương hiệu có thể thể hiện các hành vi sắc thái khác nhau trong quá trình gia nhiệt và tạo hình.
Khả năng và chuẩn bị vật liệu
Sự thành công của việc tạo hình nhiệt phụ thuộc rất nhiều vào việc chuẩn bị nguyên liệu chính xác. Bắt đầu với các tấm được cắt lớn hơn một chút so với kích thước cuối cùng, quy trình này có tính đến độ co rút của vật liệu sau khi gia nhiệt. Ngoài ra, việc loại bỏ các khuyết điểm, chẳng hạn như chip hoặc vết trầy xước, trở nên cấp thiết vì những sai sót này có thể đóng vai trò là chất xúc tác tạo ra các vết nứt trên vật liệu được tạo hình. Việc đạt được bề mặt nhẵn, không có khuyết tật sẽ đảm bảo sản phẩm cuối cùng hoàn hảo và giảm thiểu rủi ro về các điểm yếu về cấu trúc.
Dụng cụ cần thiết để chuẩn bị nguyên liệu
Trang bị cho mình những công cụ thích hợp là điều kiện tiên quyết để chuẩn bị nguyên liệu hiệu quả. Các dụng cụ thiết yếu bao gồm các dụng cụ cắt chính xác để đạt được kích thước chính xác, thiết bị chà nhám để tạo ra các cạnh hoàn hảo và thiết bị an toàn như găng tay và kính bảo vệ mắt để bảo vệ khỏi các mối nguy hiểm tiềm ẩn. Một nơi làm việc được chuẩn bị tốt, được trang bị những công cụ này sẽ tạo nền tảng cho giai đoạn chuẩn bị nguyên liệu liền mạch. Mong muốn đạt được sự hoàn hảo trong bước đầu tiên này tạo tiền đề cho nỗ lực tạo hình nhiệt thành công, trong đó sự chú ý đến từng chi tiết đồng nghĩa với kết quả chất lượng.
III. Vật liệu bề mặt rắn sưởi ấm
A. Làm nóng sơ bộ
Thông tin chung:
Gia nhiệt sơ bộ tạo tiền đề cho quá trình tạo hình nhiệt bề mặt rắn thành công. Hiểu được hành vi của vật liệu trong giai đoạn quan trọng này là điều cơ bản. Làm nóng trước đảm bảo tính linh hoạt đồng đều, giúp quá trình tạo hình tiếp theo dễ dự đoán hơn.
Phương pháp sưởi ấm (Lò nướng, Hồng ngoại, v.v.):
Nhiều phương pháp sưởi ấm khác nhau được sử dụng, mỗi phương pháp đều có giá trị riêng. Lò nướng dạng tấm cung cấp khả năng tiếp xúc trực tiếp, tạo điều kiện làm nóng nhanh hơn, trong khi lò nướng lưu thông không khí mang lại môi trường được kiểm soát tốt hơn. Các tùy chọn hồng ngoại, mặc dù không được khuyến khích, vẫn phù hợp với nhựa không hàn. Việc hiệu chỉnh lò đã chọn là bắt buộc để duy trì độ chính xác và tính nhất quán.
Hiệu chỉnh lò nướng:
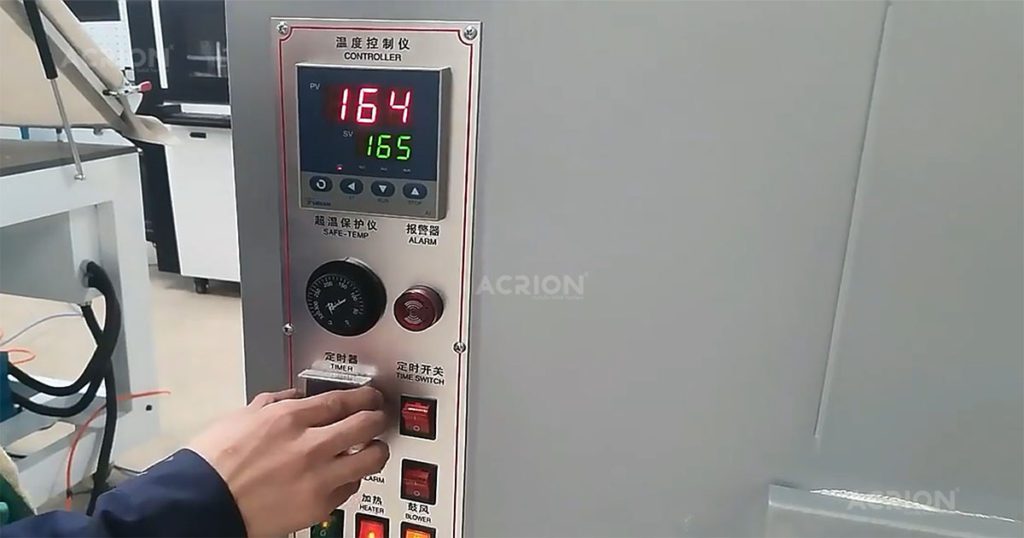
Hiệu chuẩn lò là một quá trình tỉ mỉ. Thiết lập và xác minh cài đặt nhiệt độ đảm bảo vật liệu được làm nóng chính xác. Tần suất hiệu chuẩn, đặc biệt là ở các cơ sở sản xuất cao, đảm bảo hiệu suất tối ưu và kết quả định hình nhiệt đáng tin cậy.
B. Tính linh hoạt của vật liệu
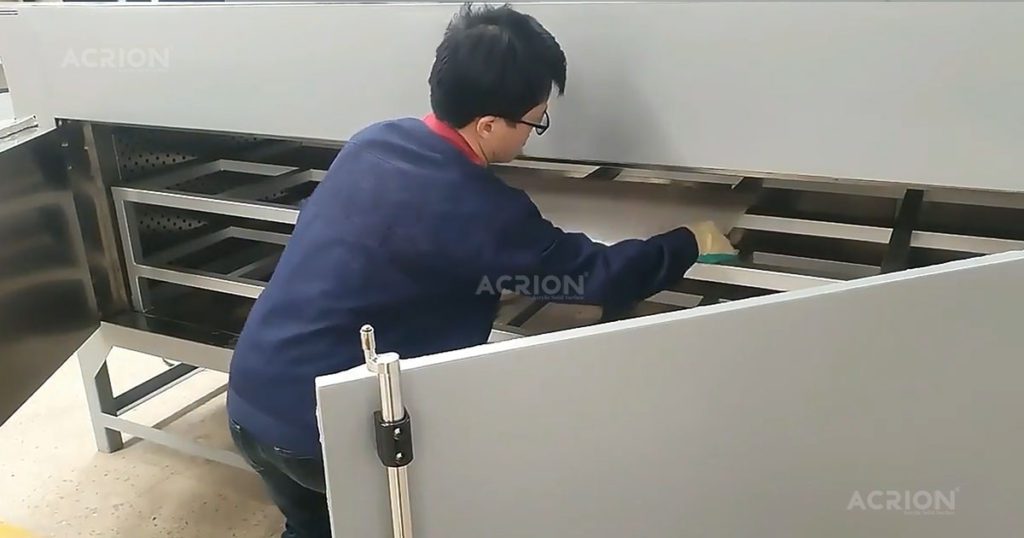
Các yếu tố ảnh hưởng đến tính linh hoạt của vật liệu:
Tính linh hoạt của vật liệu bị ảnh hưởng bởi nhiều yếu tố. Độ dày, thành phần và thời gian làm nóng trước đều đóng vai trò then chốt. Việc hiểu rõ các biến số này cho phép điều chỉnh phù hợp, tối ưu hóa tính linh hoạt cho các yêu cầu ép nóng cụ thể.
Kỹ thuật nâng cao tính linh hoạt của vật liệu:
Tối đa hóa tính linh hoạt của vật liệu đòi hỏi những cách tiếp cận chiến lược. Làm mỏng hoặc giảm lượng vật liệu một cách có chọn lọc, đặc biệt là trong các thiết kế phức tạp, có thể nâng cao tính linh hoạt mà không ảnh hưởng đến tính toàn vẹn của cấu trúc. Ngoài ra, việc tối ưu hóa nhiệt độ gia nhiệt dựa trên thành phần vật liệu đảm bảo trạng thái dẻo nhưng vẫn đàn hồi.
Gian lận
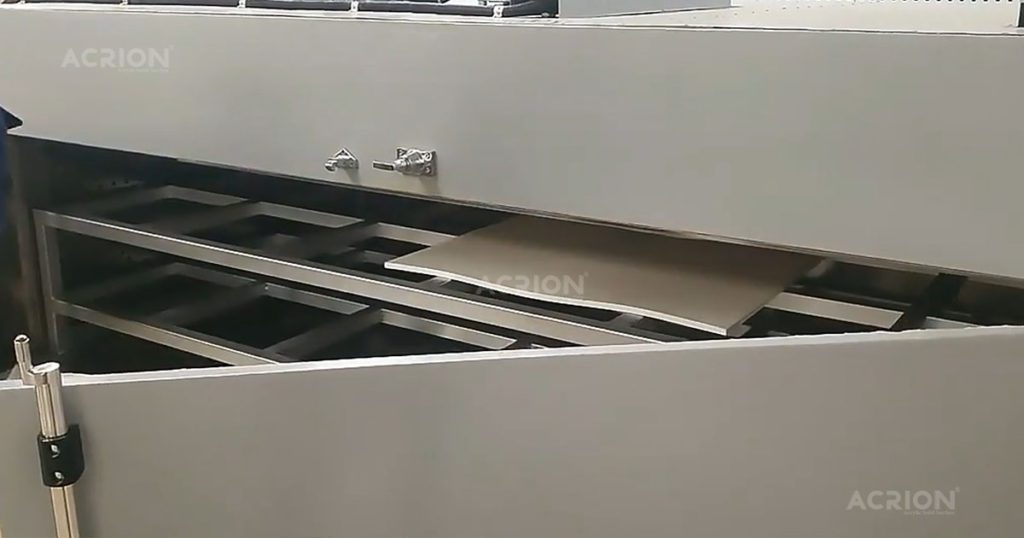
Các cách tiếp cận khác nhau để sưởi ấm:
Cảnh quan ép nóng cung cấp các phương pháp sưởi ấm đa dạng. Trong khi lò nướng dạng tấm cung cấp khả năng tiếp xúc trực tiếp, nhanh chóng thì lò nướng tuần hoàn không khí dựa vào quy trình chậm hơn, được kiểm soát. Nhiệt độ cao hơn có thể được sử dụng để đạt hiệu quả, nhưng cần thận trọng để tránh quá nhiệt, có thể ảnh hưởng đến tính toàn vẹn của vật liệu.
Đo và kiểm soát nhiệt độ:
Kiểm soát nhiệt độ chính xác là không thể thương lượng. Cho dù sử dụng cặp nhiệt điện tiếp xúc, nhiệt kế hồng ngoại hay các phương pháp tiên tiến khác, việc theo dõi và duy trì nhiệt độ mong muốn trong suốt giai đoạn gia nhiệt là rất quan trọng. Sự kiểm soát tỉ mỉ này đảm bảo sự sẵn sàng đồng nhất của vật liệu cho các bước đúc tiếp theo.
IV. Uốn và tạo hình
Kỹ thuật uốn và tạo hình
Kỹ thuật uốn hiệu quả:
Việc uốn các vật liệu có bề mặt rắn đòi hỏi sự chính xác và tinh tế. Việc sử dụng lực có kiểm soát và tận dụng tính linh hoạt của vật liệu đạt được trong giai đoạn gia nhiệt là rất quan trọng. Các kỹ thuật như uốn cạnh, tạo hình và thổi tự do được điều chỉnh theo yêu cầu đa dạng của dự án. Những phương pháp này đảm bảo tính đồng nhất trong việc tạo hình đồng thời giảm thiểu nguy cơ biến dạng.
Quá trình đúc:
Quá trình đúc đóng vai trò là nền tảng cho quá trình tạo hình nhiệt bề mặt rắn thành công. Việc sử dụng các khuôn nam và nữ được làm từ các vật liệu như ván ép hoặc MDF sẽ cung cấp một khung có cấu trúc để vật liệu phù hợp trong quá trình làm mát. Sự chú ý tỉ mỉ đến thiết kế khuôn, có tính đến các góc dự thảo và giải phóng bộ phận, đảm bảo kết quả tối ưu cho sản phẩm cuối cùng.
Phương pháp tạo hình (ép chân không, ép thủy lực)
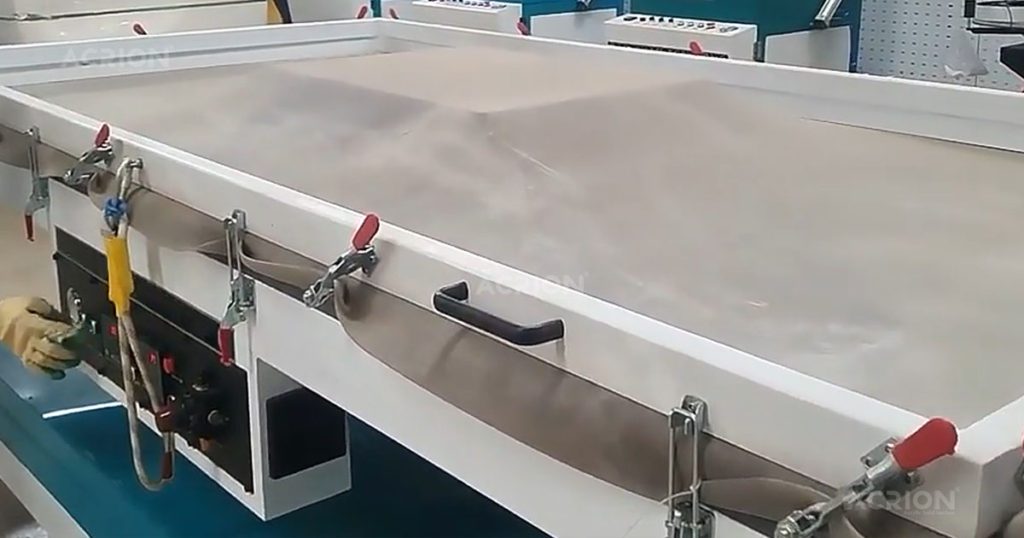
Ép chân không cho độ chính xác:
Ép chân không là một phương pháp được ưa chuộng vì độ chính xác và tính linh hoạt của nó. Quá trình này bao gồm việc sử dụng máy ép màng chân không để hút vật liệu đã được nung nóng lên bề mặt khuôn, đảm bảo các chi tiết phức tạp được tái tạo một cách trung thực. Phương pháp này đặc biệt hiệu quả đối với các thiết kế phức tạp và được áp dụng rộng rãi vì hiệu quả của nó trong sản xuất quy mô lớn.
Ép thủy lực để đảm bảo tính toàn vẹn của kết cấu:
Ép thủy lực cung cấp một giải pháp mạnh mẽ để định hình các vật liệu bề mặt rắn với tính toàn vẹn về cấu trúc được nâng cao. Áp lực thông qua hệ thống thủy lực đảm bảo nén đồng đều và giảm thiểu nguy cơ biến dạng. Cách tiếp cận này được ưu tiên cho các dự án có độ bền và độ chính xác về kích thước là tối quan trọng, chẳng hạn như các yếu tố kiến trúc và thành phần công nghiệp.
Sự thành công của việc tạo hình nhiệt bề mặt rắn phụ thuộc vào sự tích hợp liền mạch của các kỹ thuật uốn và tạo hình này. Bằng cách chọn phương pháp thích hợp dựa trên thông số kỹ thuật của dự án và đặc tính vật liệu, nhà chế tạo có thể đạt được độ chính xác và tính nhất quán đặc biệt trong sản phẩm cuối cùng.
V. Khuôn và Khuôn
Các loại khuôn
1. Khuôn đực và khuôn cái:
Sự phân đôi cơ bản trong các loại khuôn, khuôn đực chiếu vào vật liệu, trong khi khuôn cái bao bọc và định hình vật liệu. Khuôn nam thường được sử dụng cho các đường cong nông, trong khi khuôn nữ lý tưởng cho các thiết kế phức tạp. Việc chọn loại phù hợp phụ thuộc vào kết quả mong muốn và phản ứng của vật liệu đối với lực tạo hình.
2. Khuôn phù hợp:
Các khuôn phù hợp, trong đó cả hai nửa khớp với nhau một cách chính xác, đảm bảo phân bổ áp suất đồng đều trong quá trình tạo hình. Sự căn chỉnh tỉ mỉ này giúp giảm thiểu nguy cơ khuyết tật và nâng cao chất lượng tổng thể của vật liệu bề mặt rắn được hình thành. Các khuôn phù hợp được ưu tiên cho các hình dạng phức tạp và các kích thước quan trọng.
Cân nhắc thiết kế khuôn mẫu
1. Góc nháp:
Việc kết hợp các góc dự thảo trong thiết kế khuôn là yếu tố then chốt để tháo sản phẩm thành công. Những phần côn nhẹ này giúp dễ dàng lấy vật liệu đã tạo hình ra khỏi khuôn, giảm khả năng hư hỏng. Các góc phác thảo chiến lược cũng góp phần tạo nên bề mặt mịn hơn cho sản phẩm cuối cùng.
2. Đường chia tay:
Các đường phân khuôn mô tả sự tách biệt giữa các nửa khuôn. Đảm bảo căn chỉnh chính xác và độ lệch tối thiểu dọc theo các đường phân khuôn là rất quan trọng để đạt được sự liền mạch trong vật liệu tạo hình. Chú ý đến các chi tiết đường phân chia sẽ tránh được sự không hoàn hảo và nâng cao tính thẩm mỹ tổng thể.
Chuẩn bị và sử dụng khuôn
1. Xử lý bề mặt:
Trước khi sử dụng, khuôn phải được xử lý bề mặt tỉ mỉ. Điều này có thể liên quan đến việc đánh bóng, phủ hoặc sử dụng chất giải phóng để tối ưu hóa việc giải phóng vật liệu và ngăn ngừa sự bám dính. Bề mặt khuôn được xử lý tốt sẽ mang lại bề mặt hoàn hảo trên bề mặt rắn được định hình nhiệt.
2. Cân nhắc về nhiệt độ:
Duy trì nhiệt độ khuôn tối ưu là điều tối quan trọng. Những sai lệch có thể ảnh hưởng đến tốc độ làm nguội của vật liệu, ảnh hưởng đến tính chất cuối cùng của nó. Làm nóng trước khuôn, đặc biệt là trong các quy trình tạo hình tuần tự, đảm bảo kết quả nhất quán bằng cách giảm thiểu sự thay đổi về thời gian làm mát và kích thước bộ phận.
Các khuôn và khuôn tạo thành xương sống của quá trình ép nóng bề mặt rắn. Lựa chọn cẩn thận, thiết kế chính xác và chuẩn bị khuôn kỹ lưỡng là những yếu tố không thể thiếu để đạt được hình dạng và độ hoàn thiện mong muốn ở sản phẩm cuối cùng.
CHÚNG TÔI. Nguội đi
Tầm quan trọng của việc làm mát
Làm mát hiệu quả là một giai đoạn quan trọng trong quá trình tạo hình nhiệt bề mặt rắn, định hình các đặc tính cuối cùng của vật liệu. Giai đoạn làm mát nhằm mục đích giảm bớt ứng suất bên trong và củng cố cấu trúc đã hình thành. Làm mát thích hợp là điều không thể thiếu để đạt được độ chính xác về kích thước mong muốn và ngăn ngừa biến dạng ở thành phẩm.
Kỹ thuật hạ nhiệt
1. Môi trường được kiểm soát:
Tiến hành quá trình làm mát trong môi trường được kiểm soát đảm bảo tính đồng nhất. Điều này liên quan đến việc giảm thiểu các yếu tố bên ngoài như luồng không khí, biến động nhiệt độ và gió lùa có thể tác động xấu đến tốc độ làm mát. Một môi trường ổn định góp phần đảm bảo chất lượng bộ phận ổn định.
2. Làm mát dần dần:
Làm mát dần dần là bắt buộc để tránh sốc nhiệt và duy trì tính toàn vẹn của cấu trúc. Sự thay đổi nhiệt độ đột ngột có thể dẫn đến cong vênh, nứt hoặc bề mặt không đều. Việc sử dụng phương pháp làm mát có hệ thống, dù thông qua không khí xung quanh hay buồng được kiểm soát, sẽ nâng cao độ ổn định tổng thể của vật liệu.
Thời lượng và những điều cần cân nhắc trong quá trình làm mát
1. Tác động của độ dày vật liệu:
Thời gian làm mát bị ảnh hưởng bởi độ dày của vật liệu bề mặt rắn. Các phần dày hơn đòi hỏi thời gian làm mát kéo dài để đảm bảo quá trình hóa rắn hoàn toàn. Cân bằng thời gian làm mát với độ dày vật liệu là rất quan trọng để ngăn chặn việc tháo khuôn sớm, giảm nguy cơ biến dạng.
2. Kiểm tra sau làm mát:
Sau thời gian làm mát được chỉ định, việc kiểm tra tỉ mỉ là điều cần thiết. Việc xác minh rằng vật liệu đã đạt đến nhiệt độ quy định và đã ổn định đầy đủ sẽ cho phép điều chỉnh kịp thời. Việc kiểm tra cẩn thận này giúp giảm thiểu rủi ro khi xử lý vật liệu sớm, bảo tồn hình dạng mong muốn và tính toàn vẹn của cấu trúc.
Làm mát, thường là một khía cạnh bị đánh giá thấp, là yếu tố then chốt cho sự thành công của quá trình tạo hình nhiệt bề mặt rắn. Việc sử dụng các kỹ thuật làm mát tỉ mỉ phù hợp với độ dày vật liệu và điều kiện môi trường đảm bảo sản xuất các bộ phận được tạo hình nhiệt hoàn hảo, ổn định về kích thước.
VII. Lần chỉnh sửa cuối cùng
Kỹ thuật ghép nối
Độ chính xác trong mộc:
Việc ghép nối trong quá trình tạo hình nhiệt bề mặt rắn đòi hỏi sự chú ý tỉ mỉ đến từng chi tiết. Để đạt được các mối nối liền mạch đòi hỏi độ chính xác trong việc cắt và căn chỉnh các bộ phận. Việc sử dụng chất kết dính chuyên dụng dành cho vật liệu có bề mặt rắn đảm bảo các đường may chắc chắn, kín đáo. Làm sạch và chuẩn bị kỹ lưỡng các bề mặt mối nối giúp tăng cường liên kết dính, góp phần đảm bảo tính toàn vẹn về cấu trúc của cụm lắp ráp cuối cùng.
Cắt tỉa và hoàn thiện
Độ chính xác kích thước sau hình thành:
Các hoạt động cắt tỉa và hoàn thiện là rất cần thiết để tinh chỉnh các bộ phận được tạo hình bằng nhiệt theo thông số kỹ thuật dự định của chúng. Sử dụng các công cụ và kỹ thuật cắt chính xác, người vận hành cẩn thận loại bỏ vật liệu dư thừa, khôi phục các cạnh về hình dạng mong muốn. Sự chú ý nhất quán đến từng chi tiết trong giai đoạn này đảm bảo duy trì mục đích thiết kế và độ chính xác về kích thước tổng thể.
Kiểm soát chất lượng
Tiêu chuẩn đánh giá nghiêm ngặt:
Kiểm soát chất lượng đóng vai trò là điểm kiểm tra cuối cùng trong quá trình tạo hình nhiệt bề mặt rắn. Các quy trình kiểm tra nghiêm ngặt được thực hiện để đánh giá tính thẩm mỹ thị giác, độ chắc chắn của cấu trúc và việc tuân thủ các thông số kỹ thuật thiết kế. Mọi sai lệch so với tiêu chuẩn quy định đều được phát hiện và khắc phục kịp thời. Quy trình đảm bảo chất lượng tỉ mỉ này đảm bảo cung cấp các sản phẩm được định hình nhiệt chất lượng cao, hoàn hảo cho người dùng cuối.
Trong các giai đoạn cuối cùng của quá trình tạo hình nhiệt bề mặt rắn, sự nhấn mạnh vào độ chính xác còn mở rộng đến việc ghép đường may, cắt tỉa và kiểm soát chất lượng. Cam kết tuân thủ các tiêu chuẩn chính xác trong suốt các bước kết thúc này sẽ mang lại những sản phẩm hoàn thiện chuyên nghiệp đáp ứng hoặc vượt quá mong đợi của thiết kế.
VIII. Lò nướng
Tổng quan về các lò nướng khác nhau
Trong quá trình tạo hình nhiệt bề mặt rắn, việc lựa chọn lò thích hợp là một quyết định quan trọng. Ba loại chính—hồng ngoại/bức xạ, không khí nóng/đối lưu và máy ép trục lăn—cung cấp các cơ chế làm nóng riêng biệt. Lò hồng ngoại thâm nhập hiệu quả vào nhựa không chứa đầy, trong khi lò sấy không khí nóng đảm bảo sưởi ấm đồng đều. Lò ép tấm, tiếp xúc trực tiếp với các mặt vật liệu, đẩy nhanh quá trình gia nhiệt. Việc xem xét cẩn thận các yêu cầu của dự án sẽ hướng dẫn lựa chọn, đảm bảo kết quả tối ưu.
Hiệu chuẩn lò nướng
Hiệu chuẩn lò là một khía cạnh quan trọng thường bị bỏ qua. Kiểm soát nhiệt độ chính xác là điều bắt buộc để tạo hình nhiệt thành công. Kiểm tra hiệu chuẩn thường xuyên sẽ xác minh rằng nhiệt độ thực tế của lò phù hợp với điểm đặt, đảm bảo tính nhất quán qua nhiều chu kỳ. Một lò được hiệu chuẩn tốt sẽ giảm thiểu nguy cơ quá nhiệt hoặc quá nhiệt, bảo vệ tính toàn vẹn của các tấm bề mặt rắn trong quá trình ép nóng.
Thực hành tốt nhất để sử dụng lò nướng
Sử dụng lò hiệu quả bao gồm việc lập kế hoạch chiến lược và tuân thủ các phương pháp thực hành tốt nhất. Để có kết quả tối ưu, hãy làm nóng lò trước ở nhiệt độ tạo hình mong muốn, đảm bảo độ ổn định trước khi bắt đầu quy trình. Chú ý đến sự an toàn, với sự sẵn có của các thiết bị cần thiết, là điều tối quan trọng. Mặc dù các nhà chế tạo có thể muốn tăng nhiệt độ lò để làm nóng nhanh hơn, nhưng điều quan trọng là phải duy trì trong giới hạn được khuyến nghị—vượt quá 400°F (205°C) sẽ gây ra rủi ro. Ngoài ra, gia nhiệt sau, cho phép phôi tạo hình nhiệt nghỉ trong 1-2 phút sẽ hỗ trợ cân bằng nhiệt độ trước khi chuyển khuôn, một bước thường bị đánh giá thấp nhưng không thể thiếu để tạo ra kết quả tạo hình nhiệt thành công.
Khi khám phá thế giới tạo hình nhiệt bề mặt rắn, việc hiểu rõ các sắc thái của các lò khác nhau, hiệu chuẩn tỉ mỉ và tuân thủ các phương pháp thực hành tốt nhất đã được thiết lập sẽ góp phần tạo nên một quy trình tạo hình nhiệt hợp lý và hiệu quả.
IX. Thông số kỹ thuật ép nóng cho các nhãn hiệu bề mặt rắn khác nhau
So sánh các yêu cầu ép nóng của các thương hiệu khác nhau
Thông số kỹ thuật ép nóng khác nhau tùy theo nhãn hiệu bề mặt rắn, ảnh hưởng đến quá trình gia nhiệt, uốn và tạo hình. Dưới đây là so sánh toàn diện về yêu cầu ép nóng của 12 thương hiệu nổi bật:
Thương hiệu | Nhiệt độ sưởi ấm | Thời gian làm nóng | Độ dày vật liệu | Thời gian làm mát | Những cân nhắc đặc biệt |
Corian | 160°C – 170°C | 25 – 35 phút | 12 mm (1/2″) | 45 phút | Màu tối có thể bị thay đổi màu sắc |
hành tây | 160°C – 170°C | 20 – 30 phút | 12 mm (1/2″) | 40 phút | Làm mát kỹ lưỡng là rất quan trọng để duy trì hình dạng |
Tristone | 150°C | 15 – 20 phút | 9 mm (3/8″) | 30 phút | Cho phép tạo ra các thiết kế mượt mà |
nghệ thuật wilson | 160°C | 25 – 35 phút | 12 mm (1/2″) | 40 phút | Việc làm nóng toàn bộ tấm vải đúng cách là rất quan trọng |
Crion | 285°F | 18 phút | 12 mm (1/2″) | 30 phút | Quá trình ép nóng được sử dụng cho các thiết kế phức tạp |
LG Hausys | 155°C – 165°C | 20 – 30 phút | 6 mm (1/4″) | 35 phút | Các hạt trong suốt có thể không chịu nhiệt tốt |
Starone | 150°C | 18 – 25 phút | 9 mm (3/8″) | 30 phút | Thích hợp để tạo hình dạng 3D |
Hanex | 160°C – 170°C | 25 – 35 phút | 12 mm (1/2″) | 40 phút | Làm mát kỹ lưỡng là rất quan trọng để duy trì hình dạng |
Meganit | 155°C – 160°C | 20 – 30 phút | 6 mm (1/4″) | 35 phút | Tính linh hoạt của vật liệu phụ thuộc vào sự pha trộn cụ thể |
Bề mặt Aristech | 160°C | 25 – 35 phút | 12 mm (1/2″) | 40 phút | Cần thận trọng khi ép nhiệt các màu tối |
Durasein | 155°C – 165°C | 20 – 30 phút | 6 mm (1/4″) | 40 phút | Không phù hợp cho các ứng dụng ngang |
Các thông số kỹ thuật tạo hình nhiệt cho các nhãn hiệu Solid Surface khác nhau khác nhau, thể hiện bối cảnh đa dạng về nhiệt độ, thời gian và vật liệu. Các nghệ nhân phải lựa chọn cẩn thận và tuân thủ các yêu cầu cụ thể mà từng thương hiệu đưa ra để đạt được kết quả tối ưu. Bảng trên cung cấp hướng dẫn tham khảo nhanh, hỗ trợ các chuyên gia trong việc điều hướng các thông số kỹ thuật riêng biệt cho các thương hiệu Solid Surface phổ biến trong quy trình tạo hình nhiệt.
X. Phát triển quy trình và khắc phục sự cố
Bản ghi quy trình ví dụ
• Chất liệu (màu sắc và thước đo)
• Quy trình vận hành
• Mẫu hoặc chương trình trống
• Nhiệt độ lò
• ID khuôn
• Nhiệt độ khuôn (trước và sau)
• Thời gian làm nóng và làm mát
• Cắt đồ đạc hoặc chương trình
• Số lượng chi tiết được sản xuất trên khuôn
• Ngày/Giờ
• Nhiệt độ môi trường xung quanh
• Nhà điều hành
• Thành công hay thất bại
• Chất hỗ trợ xử lý được sử dụng (bột talc, sáp, v.v.)
Hồ sơ quy trình tỉ mỉ đóng vai trò là nền tảng cho một dự án tạo hình nhiệt bề mặt rắn thành công. Việc ghi lại các thông số quan trọng như chi tiết vật liệu, quy trình vận hành, thông số kỹ thuật của lò và độ phức tạp của khuôn sẽ tạo ra lộ trình cho sự nhất quán. Các yếu tố chính bao gồm màu sắc và thước đo của vật liệu, thời gian gia nhiệt và làm mát, đặc điểm khuôn và chi tiết vận hành. Nhật ký toàn diện này không chỉ đảm bảo tính đồng nhất mà còn trở thành nguồn tài nguyên vô giá để xác định các thay đổi kỹ thuật theo thời gian.
Tối ưu hóa quá trình ép nóng
Việc nâng cao tỷ lệ sản xuất đòi hỏi một cách tiếp cận chiến lược bắt nguồn từ việc hiểu rõ các yếu tố hạn chế. Cho dù sử dụng lò ép cho nhiều khuôn hay lò tuần hoàn không khí phục vụ cho một khuôn duy nhất, mỗi loại đều có ưu điểm riêng. Việc điều chỉnh nhiệt độ tạo hình ảnh hưởng đến độ cứng của vật liệu, mang lại khả năng kiểm soát các vòng cung tự nhiên. Giảm thiểu biến dạng là mấu chốt — ưu tiên vật liệu trượt khi kéo và chọn nén thay vì kéo để đảm bảo kết quả tối ưu. Đi sâu vào sự cân bằng vật liệu khuôn, sự thay đổi màu sắc trong quá trình gia nhiệt và các biện pháp phòng ngừa như làm nóng các tấm phẳng đều góp phần vào quá trình tạo hình nhiệt được tối ưu hóa.
Khắc phục sự cố thường gặp
Những thách thức về định hình nhiệt đòi hỏi một cách tiếp cận khắc phục sự cố có hệ thống. Việc tẩy trắng, thường xuất phát từ nhiệt độ không đủ, đòi hỏi phải kiểm tra kỹ lưỡng các điểm đặt, chức năng của lò và các điều kiện làm nóng trước. Làm mát bề mặt trước khi tạo hình đòi hỏi phải quản lý thời gian tỉ mỉ. Việc vượt quá mức rút tối đa đòi hỏi phải đánh giá độ kín khi uốn, mức độ giãn dài và khả năng kẹt phôi. Giải quyết nếp nhăn liên quan đến việc xem xét kỹ lưỡng mức độ nén và thiết kế khuôn. Hiện tượng rách có thể xảy ra do chất lượng cạnh trống, độ chụm hoặc khả năng màu vượt quá. Các vấn đề về chà nhám bề mặt khiến việc đánh giá độ hoàn thiện của khuôn nhanh chóng, với các hạt màu lớn hơn đòi hỏi phải xem xét cẩn thận.
Tóm lại, việc nắm vững quy trình ép nóng bề mặt rắn không chỉ đòi hỏi sự hiểu biết về mặt lý thuyết mà còn phải cam kết ghi lại, tối ưu hóa và khắc phục sự cố. Sự hiểu biết sâu sắc về các khía cạnh này giúp các nhà chế tạo có thể vượt qua các thách thức và cung cấp một cách nhất quán các sản phẩm được tạo hình nhiệt chất lượng cao.
XI. Cân nhắc an toàn
Thiết bị bảo hộ
Việc đảm bảo một môi trường ép nóng an toàn bắt đầu bằng việc lựa chọn và sử dụng tỉ mỉ các thiết bị bảo vệ. Các nhà chế tạo phải tuân thủ các quy trình an toàn nghiêm ngặt, bao gồm việc bắt buộc sử dụng găng tay chịu nhiệt, bảo vệ mắt và quần áo chống cháy. Một không gian làm việc thông thoáng được trang bị thiết bị bảo hộ cá nhân (PPE) thích hợp sẽ giảm thiểu nguy cơ bỏng, trầy xước và tiếp xúc với khói độc hại. Ưu tiên sử dụng và bảo trì nhất quán các thiết bị bảo hộ là điều bắt buộc để duy trì một môi trường làm việc an toàn.
Nguyên tắc an toàn vị trí
Việc thiết lập các hướng dẫn an toàn cho từng địa điểm cụ thể là điều tối quan trọng trong việc giảm thiểu các mối nguy hiểm liên quan đến quá trình tạo hình nhiệt bề mặt rắn. Không gian làm việc phải được trang bị lối thoát hiểm, thiết bị chữa cháy và trạm sơ cứu ở vị trí chiến lược để tiếp cận nhanh chóng. Biển báo rõ ràng nêu chi tiết các quy trình an toàn, thông tin liên hệ khẩn cấp và hướng dẫn quy trình giúp nâng cao nhận thức về tình huống. Ngoài ra, các buổi huấn luyện và diễn tập an toàn thường xuyên đảm bảo rằng nhân viên thành thạo các quy trình khẩn cấp. Việc chủ động thực hiện các biện pháp an toàn, cùng với đào tạo liên tục, tạo thành nền tảng cho môi trường làm việc an toàn trong các cơ sở ép nóng bề mặt rắn.
XII. Phần kết luận
Tóm tắt các bước chính
Tóm lại, việc nắm vững quy trình ép nóng bề mặt rắn đòi hỏi một cách tiếp cận tỉ mỉ, từ khâu chuẩn bị vật liệu cho đến công đoạn hoàn thiện cuối cùng. Các nhà chế tạo phải ưu tiên độ chính xác trong việc cắt vật liệu, tuân thủ các kỹ thuật gia nhiệt tối ưu và sử dụng các phương pháp tạo hình hợp lý. Việc sử dụng các khuôn được thiết kế tốt, các chiến lược làm mát hiệu quả và chú ý đến các công đoạn cuối cùng, bao gồm cả đường nối và kiểm soát chất lượng, đảm bảo tạo ra các bề mặt được định hình nhiệt hoàn hảo.
Xu hướng tương lai trong ép nóng bề mặt rắn
Nhìn về phía trước, lĩnh vực tạo hình nhiệt bề mặt rắn đã sẵn sàng cho những tiến bộ đáng kể. Những cải tiến về thành phần vật liệu, cùng với công nghệ gia nhiệt tiên tiến, hứa hẹn nâng cao tính linh hoạt và hiệu quả trong quy trình ép nóng. Các ứng dụng tự động hóa và trí tuệ nhân tạo có thể hợp lý hóa quá trình sản xuất, mang lại thời gian quay vòng nhanh hơn và độ chính xác cao hơn. Khi các vấn đề về môi trường ngày càng trở nên quan trọng, hãy mong đợi ngành này khám phá các vật liệu thân thiện với môi trường và các phương pháp thực hành bền vững, phù hợp với phong trào rộng lớn hơn hướng tới các quy trình sản xuất xanh hơn. Các nhà chế tạo phù hợp với những xu hướng mới nổi này sẽ có vị thế tốt để vượt trội trong bối cảnh năng động của quá trình tạo hình nhiệt bề mặt rắn.