The research on the color stability of acrylic solid surface needs to be carried out from three core dimensions: photochemical degradation, thermal oxidation and environmental interaction mechanism, and a systematic analysis should be conducted in combination with formula design, testing methods and actual application scenarios. The following is a detailed elaboration from three aspects: the source of color change, influencing factors and verification methods:
First, the chemical and physical mechanisms of color changes
Photo-oxidative degradation
Prolonged UV exposure is one of the main causes of solid surface discoloration, especially for acrylic countertops in kitchens and outdoor installations. The double bonds, ester groups and other functional groups in acrylic resin are prone to photochemical reactions under ultraviolet light (wavelength 290-400nm) causing molecular chain scission and pigment breakdown that accelerate acrylic countertop UV resistance degradation. For instance, ester groups may break under light to form small molecules of carboxylic acids and alcohols, leading to the breakage of molecular chains and changes in crosslinking density, which in turn causes the coating to turn yellow or fade. Dark-colored coatings (such as red and blue) absorb more light energy, and their color difference change rate is usually 2 to 3 times faster than that of light-colored coatings.
Thermal oxidation reaction
High‑temperature environments (≥ 60 ℃) significantly reduce color stability in solid surface materials, especially under prolonged stress. For example, exposing an acrylic countertop to 80 ℃ for 100 h can push ΔE beyond 3.0, whereas room‑temperature samples stay under 1.0—highlighting the gap in heat resistant acrylic surfaces performance. Thermal oxidation reactions can also cause microcracks on the coating surface, further exacerbating color deterioration.
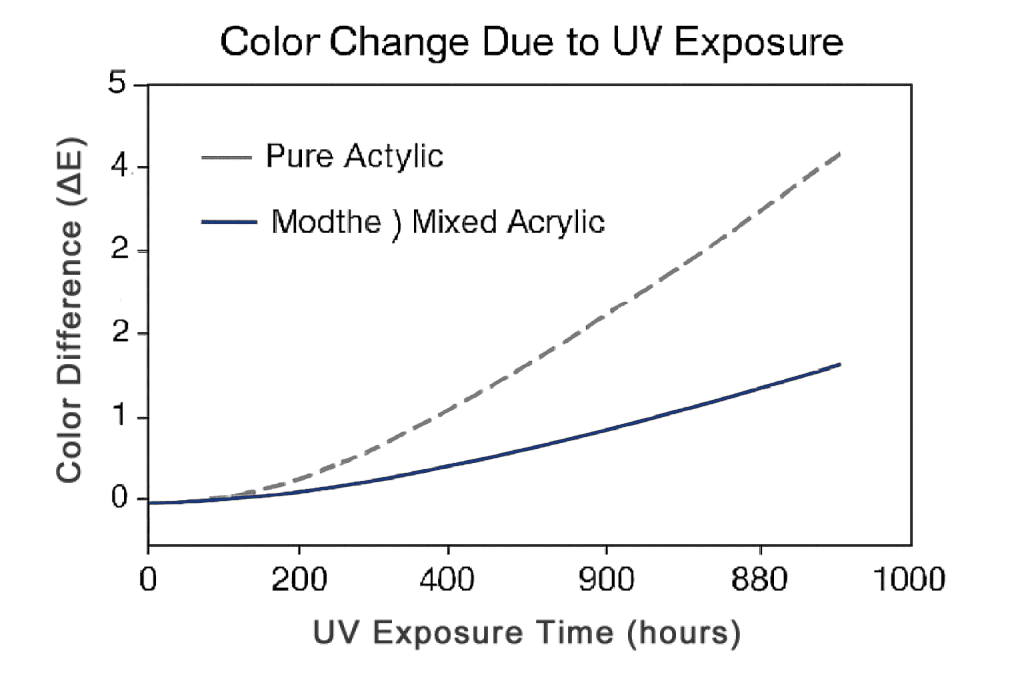
Pollutant adsorption
Nitrogen oxides, sulfur oxides, and PM2.5 particulates can linger on acrylic coatings through chemical adsorption or surface adhesion—resulting in visible anti‑pollutant adhesion and non‑yellowing solid surface degradation over time, particularly if not formulated with hydrophobic finishes. For example, in industrial pollution areas, the coating surface may present a dull tone due to the adsorption of sulfur-containing compounds, and this change is more significant in a humid environment.
Second, the key factors affecting color stability
Resin types and molecular structures
The weather resistance of pure acrylic resin is usually better than that of styrene-acrylic resin because the introduction of benzene rings in its molecular chain may increase the probability of light absorption and free radical generation. For instance, under the same lighting conditions, the color difference ΔE of the pure acrylic coating is 2.5 after 500 hours, while that of the styrene-acrylic coating may reach 4.0. In addition, the molecular weight distribution of the resin also affects color stability. Resins with a narrow distribution usually have better weather resistance.
Selection of pigments and fillers
The weather resistance of inorganic pigments (such as iron oxide red and titanium dioxide) is generally better than that of organic pigments. For instance, organic pigments such as phthalocyanine blue may undergo molecular structure changes under light exposure, leading to color fading, while the color difference change of iron oxide red under the same conditions can be ignored. The particle size and dispersion of the filler will also affect the light reflection characteristics of the coating, and thereby influence the color stability.
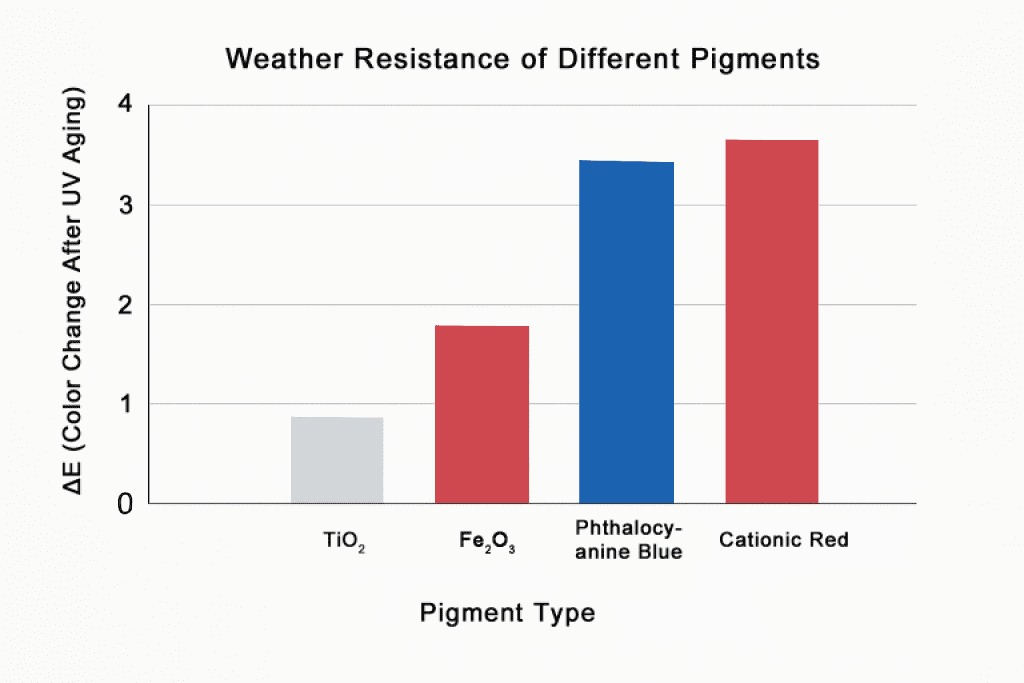
The role of the additive system
The combined use of ultraviolet absorbers (e.g. benzophenones) and HALS significantly boosts color fastness in solid surface materials, as confirmed in accelerated aging tests for acrylic surfaces. For example, the color difference ΔE of the coating with 0.5% HALS and 1.0% UV absorbent can be controlled within 1.5 under 1000 hours of xenon lamp irradiation, while the color difference of the coating without additives may exceed 5.0.
Third, testing and evaluation methods for color stability
Natural aging test
Place the coated sample outdoors and measure its color change regularly (such as every quarter). For example, in the subtropical climate zone, outdoor acrylic surface yellowing ΔE of the coating within one year may reach 3.0-5.0, and the specific value depends on the formula and orientation. Although the natural aging test is close to the actual working conditions, it has a long cycle and is greatly affected by environmental variables.
Artificial accelerated aging test
The conditions of light, temperature and humidity were simulated by using xenon lamp aging chambers (conforming to ISO 11341 standard) or ultraviolet aging chambers (conforming to ASTM G154 standard). For example, in a xenon lamp aging chamber, under the conditions of irradiance 0.51 W/m²@340nm, black plate temperature 65℃, and relative humidity 50%, the color difference ΔE of the coating after 500 hours can be used to predict its outdoor weather resistance.
For clarity, ASTM G155 acrylic surface color test and ISO 11341 chamber‐based protocols align ΔE thresholds with color fastness in solid surface materials: ΔE < 1.5 is near‐invisible, ΔE 1.5–3.0 is slight change, while ΔE > 3.0 indicates significant degradation—that is, visible acrylic countertop UV resistance loss.
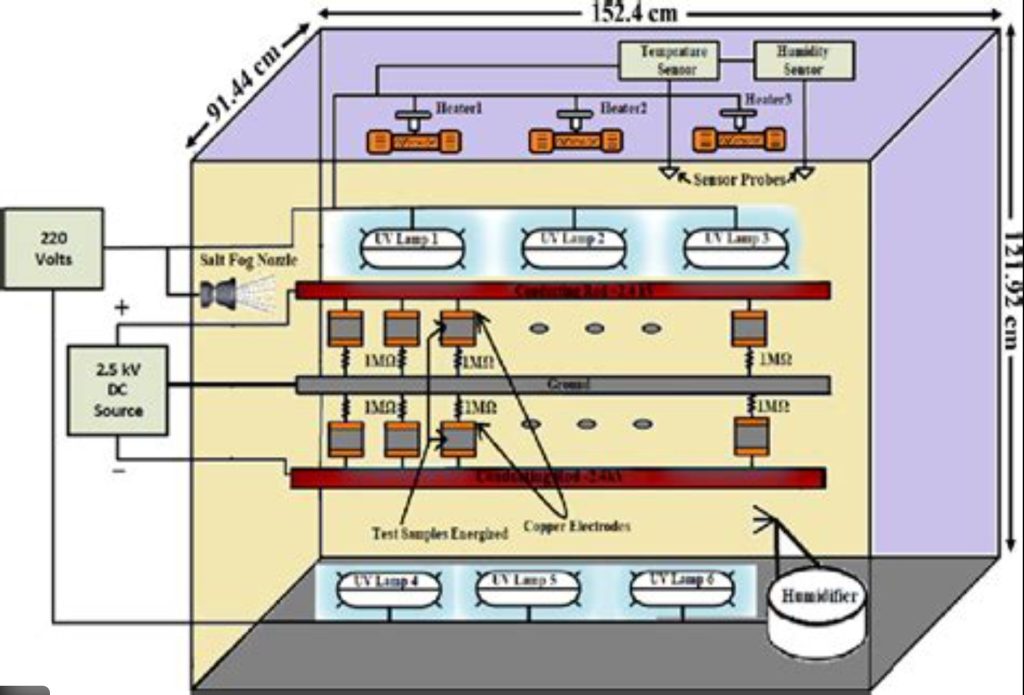
Color difference measurement and characterization
The Lab* value of the coating was measured using a spectrophotometer (such as X-Rite Ci64), and the color difference ΔE was calculated. For example, when ΔE<1.5, it is difficult for the human eye to detect the color change. When ΔE is between 1.5 and 3.0, it is a slight change. When ΔE>3.0, it is regarded as a significant change. In addition, the microstructure changes on the coating surface can also be evaluated by measuring the glossiness variations (such as a 60° Angle gloss meter).
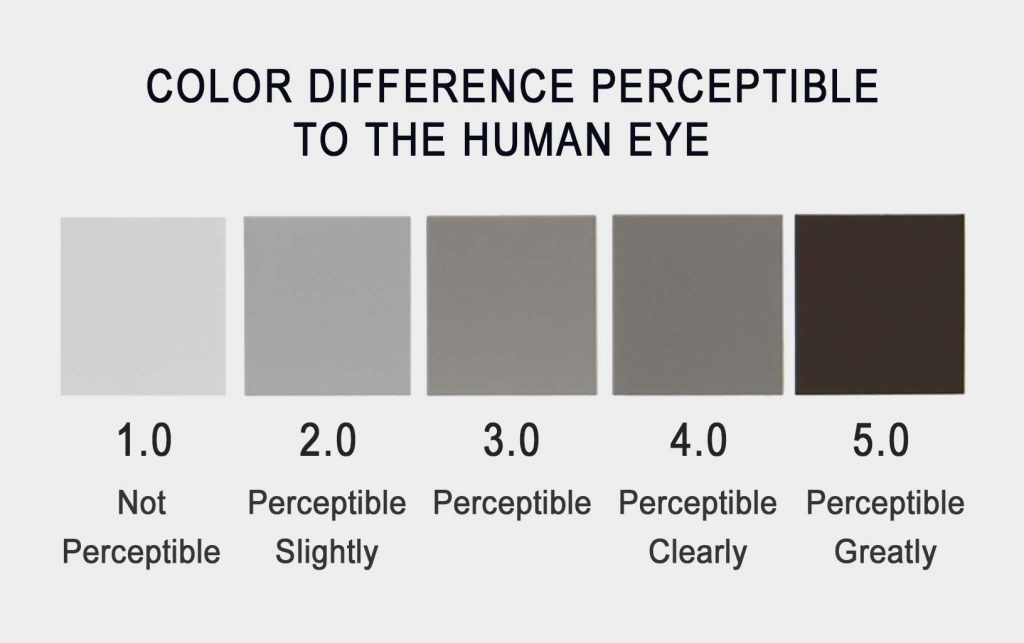
Fourth, verification of color stability in practical applications
Exterior wall coating of buildings
In high-rise buildings, the south-facing walls, which receive more sunlight, may have a coating color change rate that is more than 50% faster than that of the north-facing walls. For example, in the on-site inspection three years later, the color difference ΔE of the south-facing wall may reach 4.0, while that of the north-facing wall is only 2.5.
Traffic sign coating
The road marking coating needs to withstand tire friction, exhaust pollution and ultraviolet radiation. For instance, on expressways, the color difference ΔE of the marking coating within six months may reach 3.0, while on urban roads, due to the lower light intensity, the color difference variation may be controlled within 2.0.
Coating of outdoor furniture
Wood coatings are prone to mold in a humid environment, causing the color to turn black. For instance, in an environment with a humidity of ≥80%, coatings without added fungicides may develop mold spots within three months, while coatings with added fungicides can maintain color stability for over one year.
Fifth, strategies for enhancing color stability
Formula optimization
By adjusting resin‑to‑pigment ratios or incorporating fluorocarbon‑modified acrylic and UV stabilized solid surface agents, the result is a fade‑proof solid surface countertop with ΔE often below 1.0 in xenon lamp simulations—ideal for kitchen grade and outdoor architectural surfacing.
Surface treatment
Applying a transparent protective layer (such as a siloxane coating) on the coating surface can block ultraviolet rays and contaminants. For instance, a transparent protective layer with a thickness of 5μm can enhance the weather resistance of the coating by more than 30%.
Construction process control
Ensure that the coating thickness is uniform (such as dry film thickness ≥40μm) to avoid color differences caused by insufficient local thickness. In addition, the humidity of the construction environment should be controlled at ≤85% to prevent pinholes or sagging on the coating surface.