I. Introduction
Solid Surface Thermoforming stands as a pivotal technique in the realm of material manipulation, offering a unique avenue for crafting intricate 3-D curves and rounded shapes. This process involves heating synthetic materials, specifically solid surfaces like DuPont™ Corian®, to achieve remarkable designs unparalleled by alternatives such as quartz or granite.
Overview of Solid Surface Thermoforming
The process initiates with meticulous material preparation, ensuring its dimensions and condition meet the demanding criteria of the thermoforming journey. The subsequent stages, from controlled heating to precision molding, transform a rigid sheet into a flexible canvas awaiting the artist’s touch.
Importance and Applications
The significance of solid surface thermoforming lies in its capability to produce bespoke, three-dimensional masterpieces. Designers worldwide favor this technique for its unparalleled freedom to sculpt shapes and arcs, allowing for the creation of unique, visually striking surfaces. Whether in furniture, kitchen countertops, or commercial spaces, solid surface thermoforming emerges as a cornerstone in the domain of modern design and fabrication. This guide delves into the intricacies of this transformative process, providing insights for both novices and seasoned professionals.
Solid surface thermoforming is a widely used technique in the field of solid surface fabrication, allowing for the creation of intricate and customized designs. This process involves heating a solid surface material, such as Acrion, and shaping it into desired forms. In this guide, we will walk you through the step-by-step process of solid surface thermoforming, providing important notes and precautions along the way. It is crucial to adhere to these guidelines, review the suitability of the material for your intended use, and comply with applicable laws and regulations.
II. Material Preparation
Material Overview
Solid Surface Thermoforming hinges on meticulous material selection, predominantly employing acrylic-based sheets like DuPont™ Corian®. These materials offer a delicate balance between flexibility and durability, crucial for achieving desired forms during the thermoforming process. Understanding the specific characteristics of the chosen material is paramount, as each brand may exhibit nuanced behaviors during heating and shaping.
Material Capability and Preparation
The success of thermoforming heavily relies on precise material preparation. Initiating with sheets cut marginally larger than the final dimensions, the process accounts for material shrinkage post-heating. Additionally, eliminating imperfections, such as chips or scratches, becomes imperative, as these flaws can serve as catalysts for cracks in the formed material. Achieving a smooth, defect-free surface ensures a flawless final product and minimizes the risk of structural weaknesses.
Tools Required for Material Preparation
Arming oneself with the appropriate tools is a prerequisite for effective material preparation. Essential instruments include precision cutting tools to achieve accurate dimensions, sanding equipment for flawless edges, and safety gear, such as gloves and eye protection, to safeguard against potential hazards. A well-prepared workstation, equipped with these tools, establishes the foundation for a seamless material preparation phase. Aspiring to achieve perfection in this initial step sets the stage for a successful thermoforming endeavor, where attention to detail becomes synonymous with quality outcomes.
III. Heating Solid Surface Material
A. Preheating
General Information:
Preheating sets the stage for successful solid surface thermoforming. Understanding the material’s behavior during this critical phase is fundamental. Preheating ensures uniform flexibility, making the subsequent shaping process more predictable.
Heating Methods (Ovens, Infrared, etc.):
Various heating methods are employed, each with its merits. Platen ovens offer direct contact, facilitating faster heating, while air circulating ovens provide a more controlled environment. Infrared options, though not recommended, are suitable for unfilled plastics. Calibrating the chosen oven is imperative to maintain precision and consistency.
Calibrating the Oven:
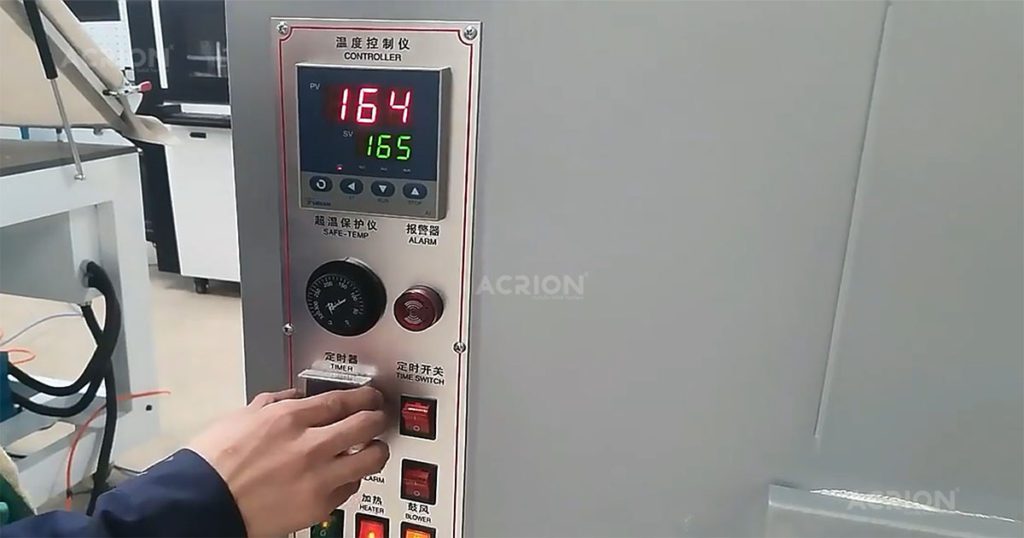
Oven calibration is a meticulous process. Establishing and verifying the temperature settings ensure the material is heated accurately. Calibration frequency, especially in high-production settings, guarantees optimal performance and reliable thermoforming outcomes.
B. Material Flexibility
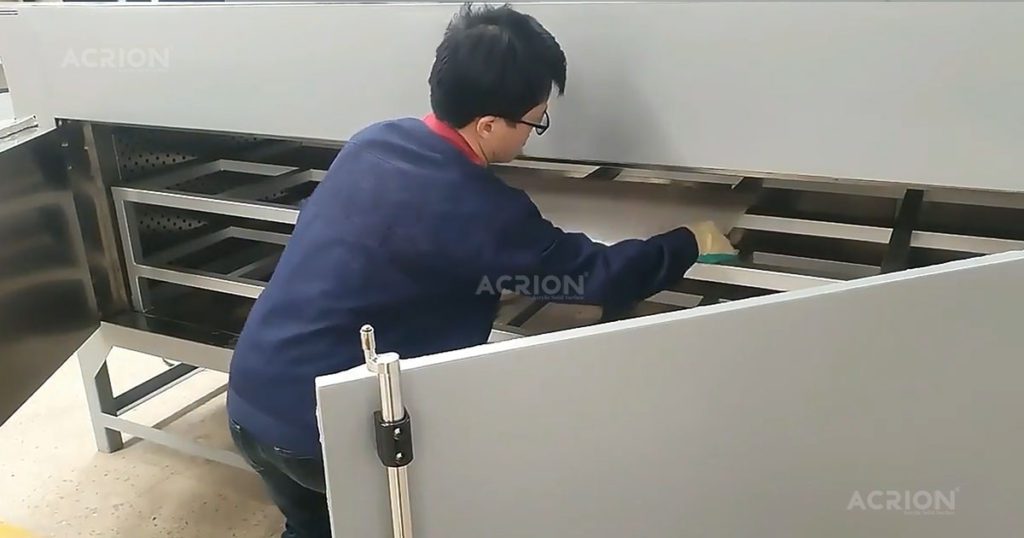
Factors Affecting Material Flexibility:
Material flexibility is influenced by multiple factors. Thickness, composition, and preheating duration all play pivotal roles. Understanding these variables allows for tailored adjustments, optimizing flexibility for specific thermoforming requirements.
Techniques to Enhance Material Flexibility:
Maximizing material flexibility demands strategic approaches. Thinning or rebating the material selectively, especially in intricate designs, can enhance flexibility without compromising structural integrity. Additionally, optimizing heating temperatures based on material composition ensures a pliable yet resilient state.
C. Heating
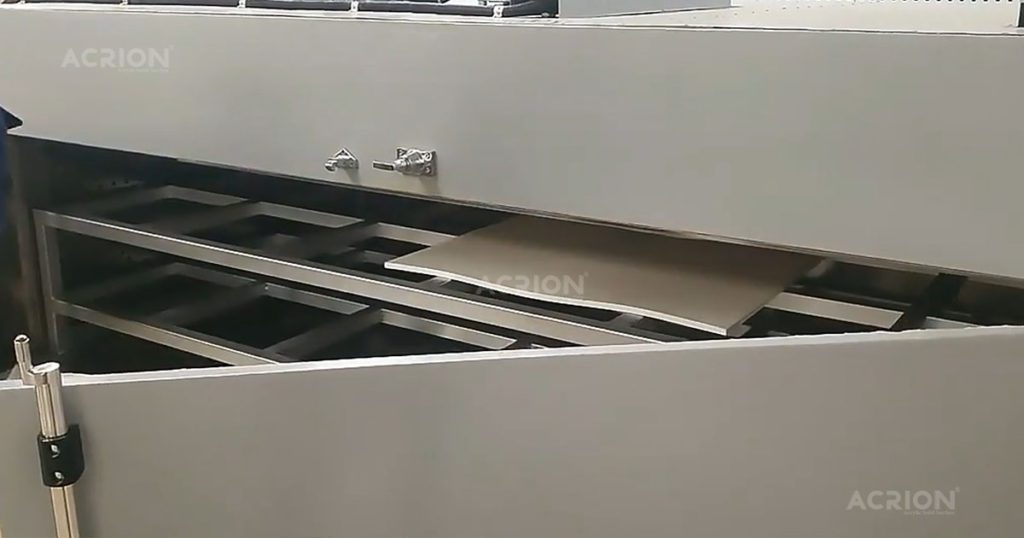
Different Approaches to Heating:
The thermoforming landscape offers diverse heating approaches. While platen ovens provide quick, direct contact, air circulating ovens rely on a slower, controlled process. Higher temperatures may be employed for efficiency, but caution is exercised to prevent overheating, which can compromise material integrity.
Temperature Measurement and Control:
Precise temperature control is non-negotiable. Whether using contact thermocouples, infrared thermometers, or other advanced methods, monitoring and maintaining the desired temperature throughout the heating phase are critical. This meticulous control ensures uniform material readiness for the subsequent molding steps.
IV. Bending and Shaping
Techniques for Bending and Shaping
Efficient Bending Techniques:
Bending solid surface materials demands precision and finesse. Employing controlled force and leveraging the material’s flexibility achieved during the heating phase is crucial. Techniques such as edge bending, drape forming, and free blowing are tailored to diverse project requirements. These methods ensure uniformity in shaping while mitigating the risk of deformities.
Molding Process:
Molding acts as the cornerstone for successful solid surface thermoforming. Utilizing male and female molds constructed from materials like plywood or MDF provides a structured framework for the material to conform to during cooling. Meticulous attention to mold design, with considerations for draft angles and part release, guarantees optimal results in the final product.
Shaping Approaches (Vacuum Pressing, Hydraulic Pressing)
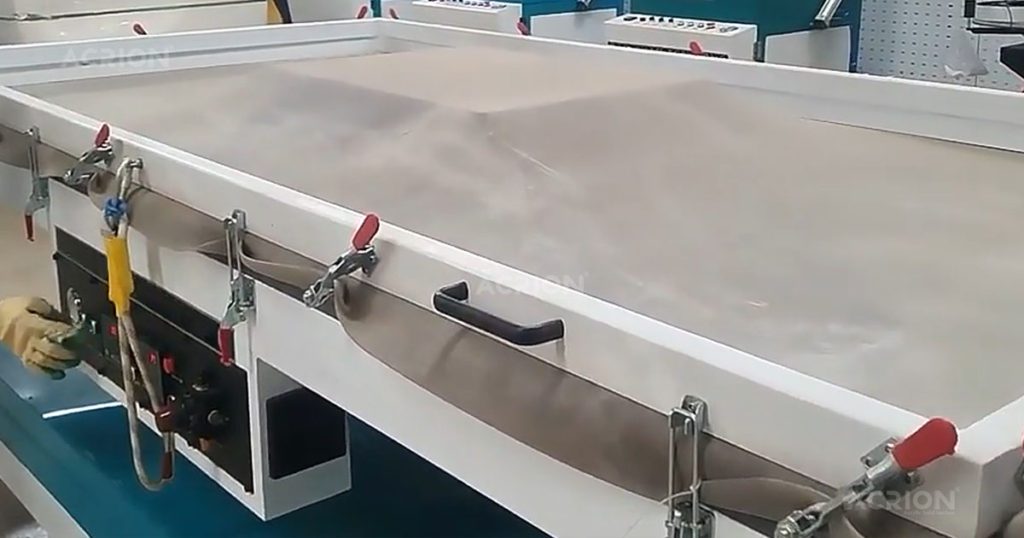
Vacuum Pressing for Precision:
Vacuum pressing is a favored approach for its precision and versatility. The process involves using a vacuum membrane press to draw the heated material onto the mold surface, ensuring intricate details are faithfully reproduced. This method is particularly effective for complex designs and is widely adopted for its efficiency in large-scale production.
Hydraulic Pressing for Structural Integrity:
Hydraulic pressing offers a robust solution for shaping solid surface materials with enhanced structural integrity. Applying pressure through hydraulic systems ensures uniform compression and minimizes the risk of deformities. This approach is preferred for projects where durability and dimensional accuracy are paramount, such as architectural elements and industrial components.
Solid surface thermoforming’s success hinges on the seamless integration of these bending and shaping techniques. By selecting the appropriate method based on project specifications and material characteristics, fabricators can achieve exceptional precision and consistency in the final product.
V. Forms and Molds
Types of Molds
1. Male and Female Molds:
The fundamental dichotomy in mold types, male molds project into the material, while female molds encase and shape the material. Male molds are often employed for shallow curves, while female molds are ideal for intricate designs. Choosing the right type hinges on the desired outcome and the material’s response to shaping forces.
2. Matched Molds:
Matched molds, where both halves interlock precisely, ensure uniform pressure distribution during shaping. This meticulous alignment minimizes the risk of defects and enhances the overall quality of the formed solid surface material. Matched molds are preferred for intricate geometries and critical dimensions.
Mold Design Considerations
1. Draft Angles:
Incorporating draft angles in mold design is pivotal for successful part release. These slight tapers facilitate easy removal of the formed material from the mold, reducing the likelihood of damage. Strategic draft angles also contribute to a smoother surface finish in the final product.
2. Parting Lines:
Parting lines delineate the separation between mold halves. Ensuring precise alignment and minimal deviation along parting lines is crucial for achieving seamlessness in the formed material. Attention to parting line details avoids imperfections and enhances the overall aesthetic appeal.
Preparation and Use of Molds
1. Surface Treatment:
Prior to use, molds should undergo meticulous surface treatment. This may involve polishing, coating, or application of release agents to optimize material release and prevent adhesion. A well-treated mold surface translates to a flawless finish on the thermoformed solid surface.
2. Temperature Considerations:
Maintaining an optimal mold temperature is paramount. Deviations can impact the material’s cooling rate, affecting its final properties. Preheating molds, especially in sequential forming processes, ensures consistent results by minimizing variations in cooling times and part dimensions.
Forms and molds constitute the backbone of the solid surface thermoforming process. Careful selection, precise design, and thorough preparation of molds are indispensable elements for achieving the desired form and finish in the final product.
VI. Cool Down
Importance of Cooling
Efficient cooling is a critical phase in the solid surface thermoforming process, shaping the material’s final properties. The cooling stage serves to relieve internal stresses and solidify the formed structure. Proper cooling is integral to achieving the desired dimensional accuracy and preventing deformities in the finished product.
Cool Down Techniques
1. Controlled Environment:
Conducting the cooling process in a controlled environment ensures uniformity. This involves mitigating external factors such as airflow, temperature fluctuations, and drafts, which can adversely impact the cooling rate. A stable environment contributes to consistent part quality.
2. Gradual Cooling:
Gradual cooling is imperative to avoid thermal shock and maintain structural integrity. Abrupt temperature changes can lead to warping, cracking, or surface irregularities. Employing a systematic approach to cooling, whether through ambient air or controlled chambers, enhances the material’s overall stability.
Duration and Considerations during Cooling
1. Material Thickness Impact:
The cooling duration is influenced by the thickness of the solid surface material. Thicker sections necessitate extended cooling times to ensure thorough solidification. Balancing cooling duration with material thickness is crucial to prevent premature removal from molds, reducing the risk of deformation.
2. Post-Cooling Inspection:
After the designated cooling period, a meticulous inspection is essential. Verifying that the material has reached the prescribed temperature and has adequately settled allows for timely adjustments. This careful examination mitigates the risk of handling the material prematurely, preserving the desired form and structural integrity.
Cooling, often an underestimated aspect, is pivotal to the success of solid surface thermoforming. Employing meticulous cooling techniques tailored to material thickness and environmental conditions ensures the production of flawless, dimensionally stable thermoformed parts.
VII. Final Touches
Seaming Techniques
Precision in Joinery:
Seaming in solid surface thermoforming demands meticulous attention to detail. Achieving seamless joints requires precision in cutting and aligning parts. Utilizing specialized adhesives formulated for solid surface materials ensures robust, inconspicuous seams. Thorough cleaning and preparation of joint surfaces enhance adhesive bonding, contributing to the structural integrity of the final assembly.
Trimming and Finishing
Post-Forming Dimensional Accuracy:
Trimming and finishing operations are essential to refine thermoformed parts to their intended specifications. Employing precision cutting tools and techniques, operators carefully remove excess material, restoring edges to the desired shape. Consistent attention to detail during this phase ensures the preservation of design intent and overall dimensional accuracy.
Quality Control
Stringent Evaluation Standards:
Quality control serves as the final checkpoint in the solid surface thermoforming process. Rigorous inspection protocols are implemented to assess visual aesthetics, structural soundness, and adherence to design specifications. Any deviations from the prescribed standards are identified and rectified promptly. This meticulous quality assurance process guarantees the delivery of flawless, high-quality thermoformed products to end-users.
In the final stages of solid surface thermoforming, the emphasis on precision extends to seaming, trimming, and quality control. A commitment to exacting standards throughout these concluding steps results in professionally finished products that meet or exceed design expectations.
VIII. Ovens
Overview of Different Ovens
In solid surface thermoforming, selecting the appropriate oven is a pivotal decision. Three main types—infrared/radiant, hot air/convection, and platen press—offer distinct heating mechanisms. Infrared ovens efficiently penetrate unfilled plastics, while hot air ovens ensure uniform heating. Platen press ovens, making direct contact with material sides, expedite the heating process. Careful consideration of project requirements guides the choice, ensuring optimal results.
Calibration of Ovens
Oven calibration is a critical aspect often overlooked. Precise temperature control is imperative for successful thermoforming. Regular calibration checks verify that the oven’s actual temperature aligns with the set point, guaranteeing consistency across multiple cycles. A well-calibrated oven minimizes the risk of overheating or underheating, safeguarding the integrity of solid surface sheets during the thermoforming process.
Best Practices for Oven Use
Efficient oven use involves strategic planning and adherence to best practices. For optimal results, preheat the oven to the desired forming temperature, ensuring stability before initiating the process. Attention to safety, with the availability of necessary equipment, is paramount. While fabricators may be tempted to increase oven temperatures for faster heating, it is crucial to stay within recommended limits—exceeding 400°F (205°C) poses risks. Additionally, post-heating, allowing the thermoformed blank to rest for 1-2 minutes aids temperature equilibration before mold transfer, a step often underestimated but integral to successful thermoforming outcomes.
In navigating the world of solid surface thermoforming, understanding the nuances of different ovens, meticulous calibration, and adherence to established best practices collectively contribute to a streamlined and effective thermoforming process.
IX. Thermoforming Specifications for Different Brands of Solid Surface
Comparison of Thermoforming Requirements for Various Brands
Thermoforming specifications vary across solid surface brands, impacting the heating, bending, and shaping processes. Below is a comprehensive comparison of thermoforming requirements for 12 prominent brands:
Brand | Heating Temperature | Heating Time | Material Thickness | Cooling Time | Special Considerations |
Corian | 160°C – 170°C | 25 – 35 min | 12 mm (1/2″) | 45 min | Dark colors may experience color change |
Acrion | 160°C – 170°C | 20 – 30 min | 12 mm (1/2″) | 40 min | Thorough cooling is crucial for maintaining shape |
Tristone | 150°C | 15 – 20 min | 9 mm (3/8″) | 30 min | Allows for creating smooth-flowing designs |
Wilsonart | 160°C | 25 – 35 min | 12 mm (1/2″) | 40 min | Proper heating of the entire sheet is crucial |
Krion | 285°F | 18 min | 12 mm (1/2″) | 30 min | Thermoforming process used for intricate designs |
LG Hausys | 155°C – 165°C | 20 – 30 min | 6 mm (1/4″) | 35 min | Transparent particulates may not thermoform well |
Staron | 150°C | 18 – 25 min | 9 mm (3/8″) | 30 min | Suitable for creating 3D shapes |
Hanex | 160°C – 170°C | 25 – 35 min | 12 mm (1/2″) | 40 min | Thorough cooling is crucial for maintaining shape |
Meganite | 155°C – 160°C | 20 – 30 min | 6 mm (1/4″) | 35 min | Material flexibility depends on the specific blend |
Aristech Surfaces | 160°C | 25 – 35 min | 12 mm (1/2″) | 40 min | Caution required when thermoforming dark colors |
Durasein | 155°C – 165°C | 20 – 30 min | 6 mm (1/4″) | 40 min | Not suitable for horizontal applications |
The thermoforming specifications for different brands of Solid Surface vary, presenting a diverse landscape of temperature, time, and material considerations. Artisans must carefully select and adhere to the specific requirements outlined by each brand to achieve optimal results. The table above provides a quick reference guide, aiding professionals in navigating the distinct specifications for popular Solid Surface brands in the thermoforming process.
X. Process Development and Troubleshooting
Example Process Record
• Material (color and gauge)
• Operating procedure
• Blank template or program
• Oven temperature
• Mold ID
• Mold temperature (before and after)
• Heating and cooling time
• Trim fixture or program
• Number of parts produced on mold
• Day/Time
• Ambient temperature
• Operator
• Success or failure
• Process aids used (talc, wax, etc.)
A meticulous process record serves as the cornerstone of a successful solid surface thermoforming venture. Documenting critical parameters such as material details, operating procedures, oven specifications, and molding intricacies creates a roadmap for consistency. Key elements encompass material color and gauge, heating and cooling times, mold characteristics, and operator details. This comprehensive log not only ensures uniformity but also becomes an invaluable resource for identifying technique changes over time.
Optimization of Thermoforming Process
Enhancing production rates requires a strategic approach rooted in understanding limiting factors. Whether employing a platen oven for multiple molds or an air circulating oven catering to a single mold, each has its merits. Adjusting forming temperature influences material stiffness, providing control over natural arcs. Minimizing deformation is pivotal—favoring material sliding over stretching and choosing compression over stretching ensures optimal results. Delving into mold material trade-offs, color shifts during heating, and preemptive measures like heating flat sheets all contribute to an optimized thermoforming process.
Troubleshooting Common Issues
Thermoforming challenges demand a systematic troubleshooting approach. Whitening, often stemming from insufficient temperature, necessitates thorough examination of set points, oven functionality, and preheating conditions. Surface cooling before forming requires meticulous time management. Exceeding maximum draws necessitates assessing bend tightness, elongation levels, and potential blank entrapment. Addressing wrinkling involves scrutinizing compression levels and mold design. Tearing may result from blank edge quality, pinching, or exceeded color capabilities. Surface sanding concerns prompt mold finish evaluations, with larger particle colors demanding careful consideration.
In conclusion, mastering the solid surface thermoforming process requires not just a theoretical understanding but a commitment to documenting, optimizing, and troubleshooting. A nuanced comprehension of these facets empowers fabricators to navigate challenges and consistently deliver high-quality thermoformed products.
XI. Safety Considerations
Protective Equipment
Ensuring a secure thermoforming environment begins with the meticulous selection and utilization of protective equipment. Fabricators must adhere to stringent safety protocols, including the mandatory use of heat-resistant gloves, eye protection, and flame-retardant clothing. A well-ventilated workspace equipped with appropriate personal protective equipment (PPE) mitigates the risk of burns, abrasions, and exposure to harmful fumes. Prioritizing the consistent use and maintenance of protective gear is imperative to uphold a safe working environment.
Location Safety Guidelines
Establishing location-specific safety guidelines is paramount in minimizing hazards associated with solid surface thermoforming. Workspaces must be equipped with emergency exits, firefighting equipment, and first aid stations strategically located for swift access. Clear signage detailing safety protocols, emergency contact information, and procedural instructions enhances situational awareness. Additionally, regular safety drills and training sessions ensure that personnel are well-versed in emergency procedures. The proactive implementation of safety measures, coupled with continuous education, forms the cornerstone of a secure working environment in solid surface thermoforming facilities.
XII. Conclusion
Recap of Key Steps
In conclusion, mastering the solid surface thermoforming process demands a meticulous approach, from material preparation to the final touches. Fabricators must prioritize precision in material cutting, adhere to optimal heating techniques, and employ judicious shaping methods. The use of well-designed molds, effective cooling strategies, and a vigilant eye on final touches, including seaming and quality control, ensures the production of impeccable thermoformed surfaces.
Future Trends in Solid Surface Thermoforming
Looking ahead, the field of solid surface thermoforming is poised for significant advancements. Innovations in material compositions, coupled with state-of-the-art heating technologies, promise enhanced flexibility and efficiency in the thermoforming process. Automation and artificial intelligence applications may streamline production, offering faster turnarounds and heightened precision. As environmental considerations become increasingly pivotal, expect the industry to explore eco-friendly materials and sustainable practices, aligning with the broader movement toward greener manufacturing processes. Fabricators who stay attuned to these emerging trends will be well-positioned to excel in the dynamic landscape of solid surface thermoforming.